Our customers
The Problem
Without a modern maintenance software, missing transparency, duplicate inventory, and last-minute scrambling turn spare parts into a bottleneck – causing downtime, delays, and unnecessary costs.
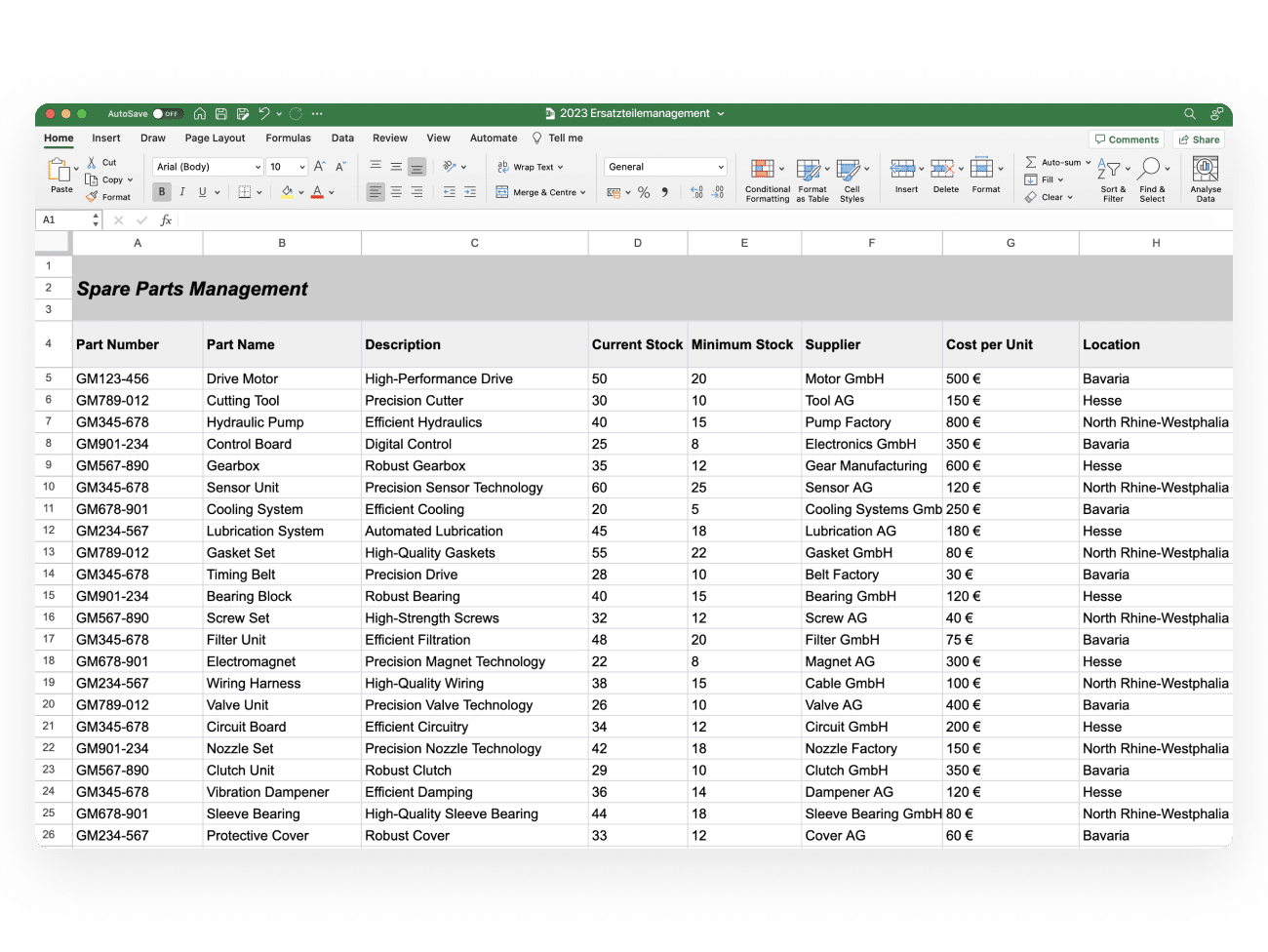
Before
- Scattered: Spare parts are stored in different locations – no one has the full picture.
- Unclear: No one knows for sure if a part is available, where it is, or if it fits.
- Uncontrolled: Orders for new parts are placed on guesswork or duplicated – because reliable inventory data is missing.
- Time-consuming: Technicians waste time on every job searching for parts or chasing down answers.
- Costly: Missing parts lead to emergency orders, delays, and extended downtime.
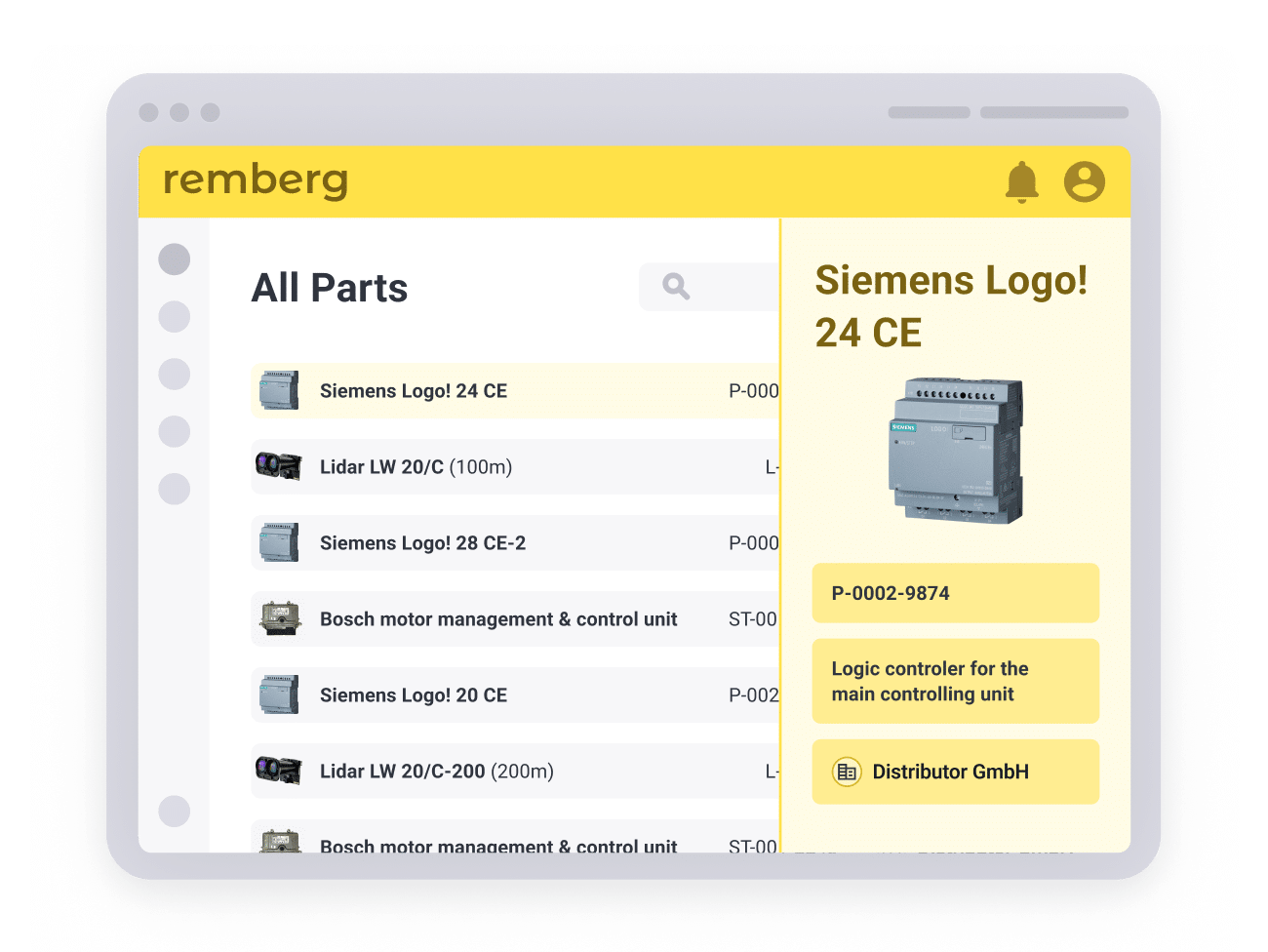
After
- Centralised: All spare parts and consumable are digitally documented – including storage location, stock levels, and links to assets and equipment.
- Transparent: You can instantly see what parts are available and where - directly from the asset view.
- Structured: Defined storage locations, clear stock levels, and usage history provide the foundation for better planning.
- Efficient: Parts are linked directly to work orders - no more chasing information or wasting time searching.
- Cost-conscious: Fewer emergency orders, less overstock, and reduced downtime.
Always know what’s in stock – and where it is
No more searching, guessing, or hoarding. With remberg, all spare and consumable parts are managed centrally – including storage location, stock levels, and categories. You see at a glance if a part is available, and exactly where to find it. That saves time and money, reduces frustration, and puts an end to spreadsheets, scattered shelves, and the classic: “Pretty sure we’ve got one... somewhere.”
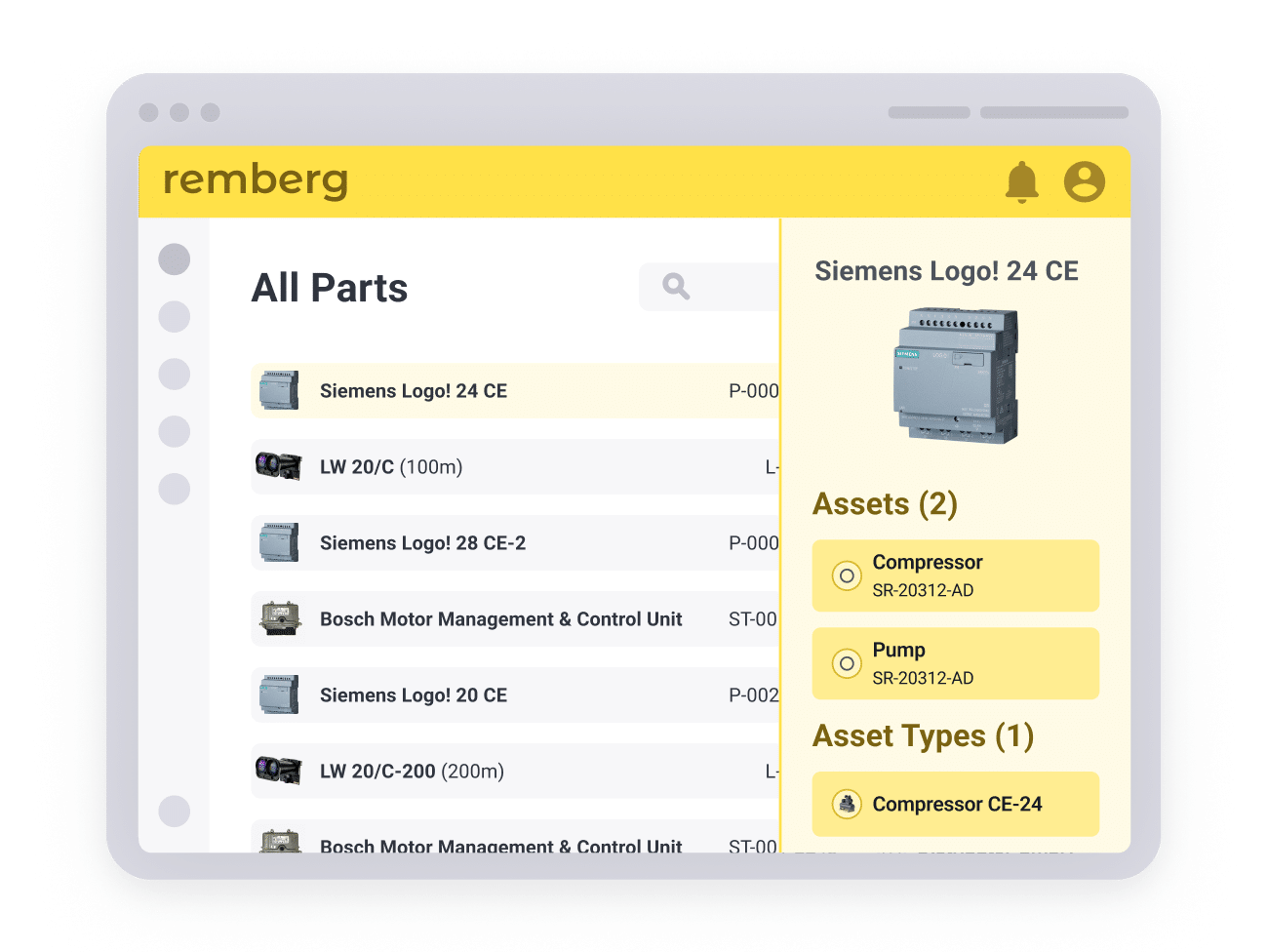
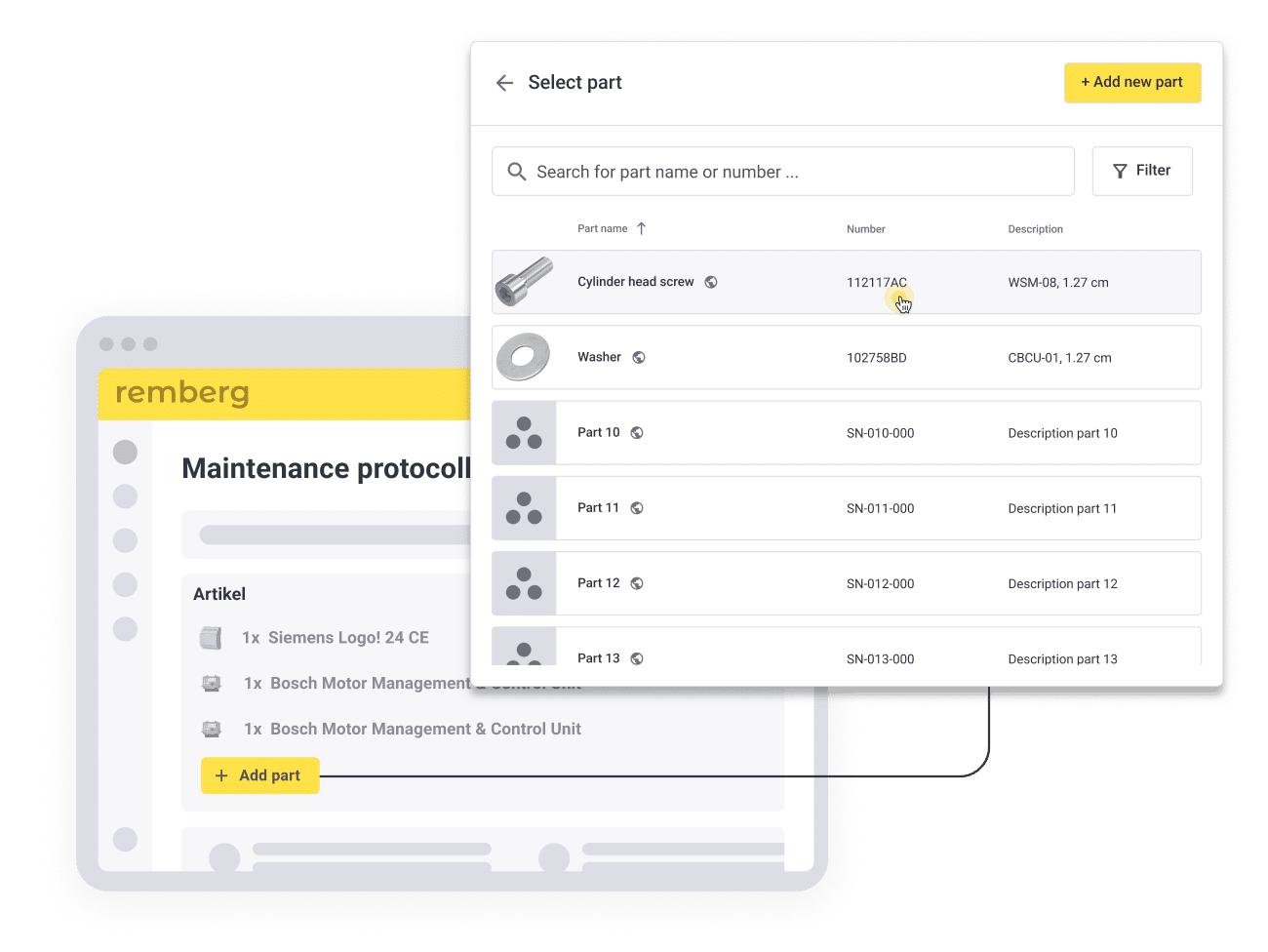
Link spare parts directly to assets and work orders
In remberg, spare and consumable parts are directly connected to your assets, maintenance schedules, work orders, and checklists. When an issue occurs, you instantly see which part is needed – and whether it’s in stock. That means faster, more reliable responses, and a team that works more efficiently without extra questions or unnecessary detours.
Access parts on the go – right where the work happens
Search, scan, and log parts with just your smartphone or tablet. Whether you're on the shop floor or out in the field, the remberg mobile app lets you scan assets via QR code, check part availability, and document material usage on the spot. No more trips to the terminal, no more paper notes, no more logging things later in the evening.
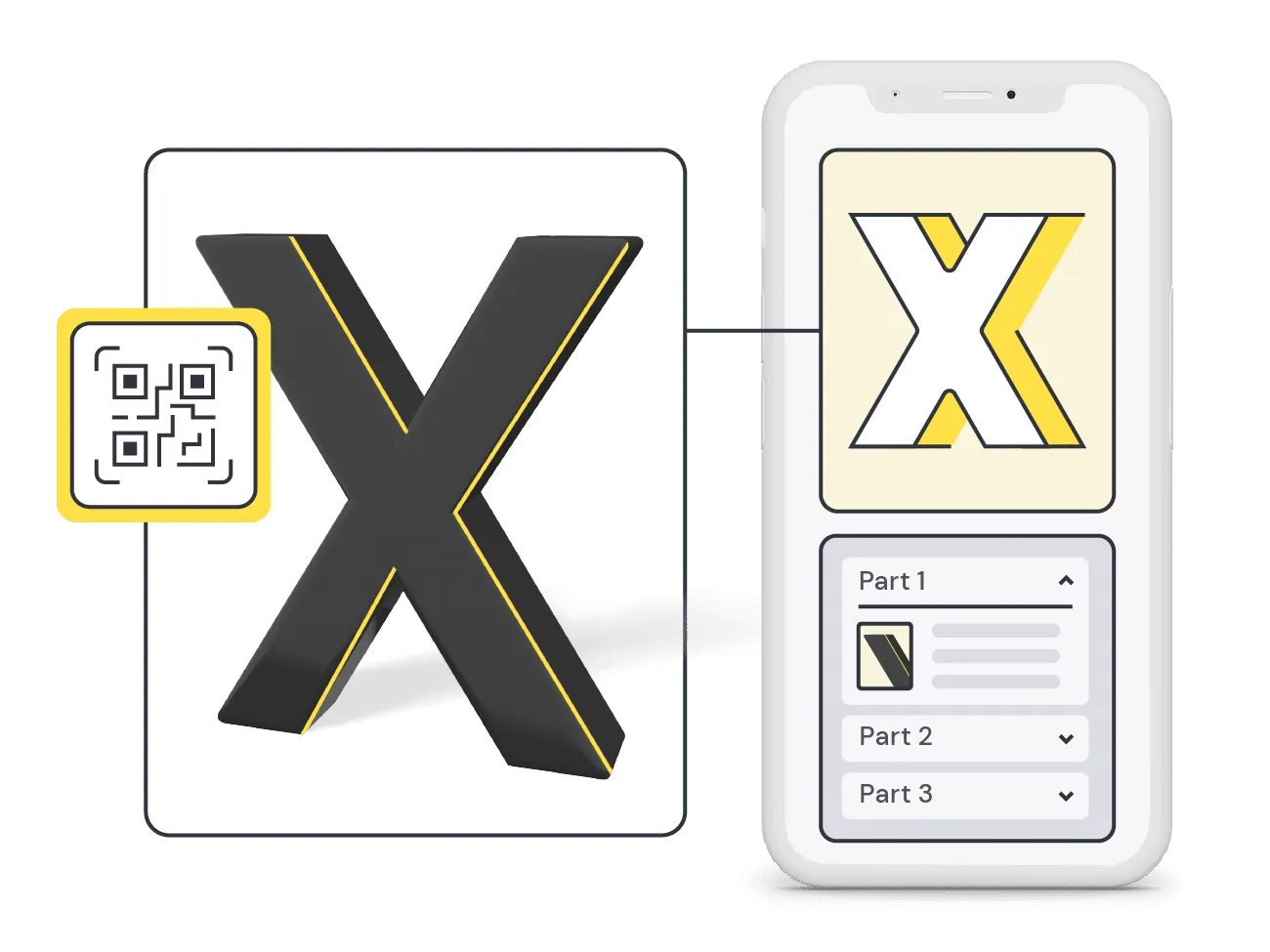
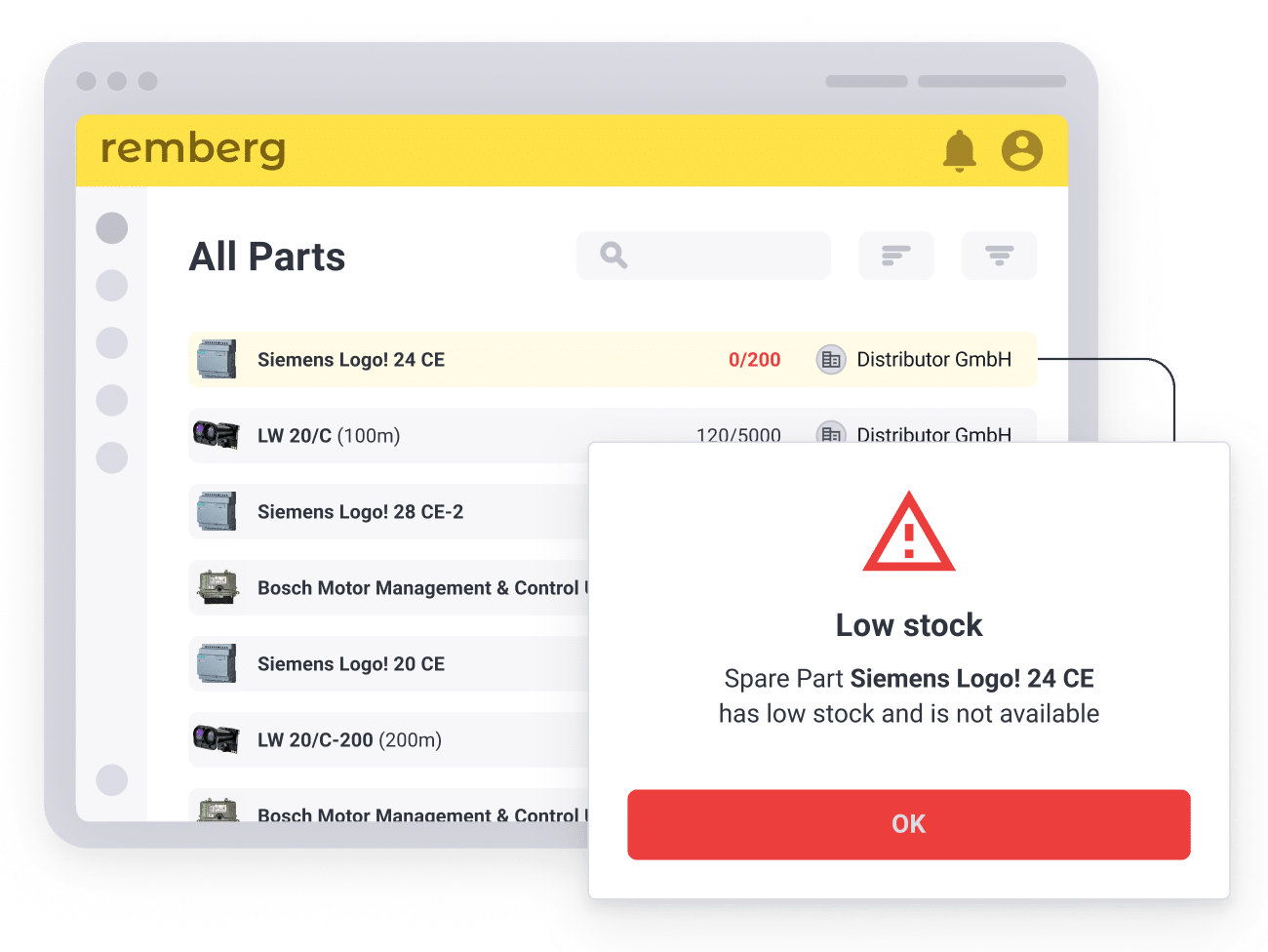
Plan like a pro – instead of reacting last minute
Get a clear overview of your inventory across all locations, plan spare parts ahead of time for upcoming maintenance tasks, and respond early to potential shortages. With remberg, you're not just managing stock – you're actively controlling it.
Track every part movement – with full transparency
remberg gives you complete visibility into what’s happening with your spare parts. Every inventory change is documented clearly and consistently. That means fewer misunderstandings, more clarity for your team, and no more scrambling during audits.
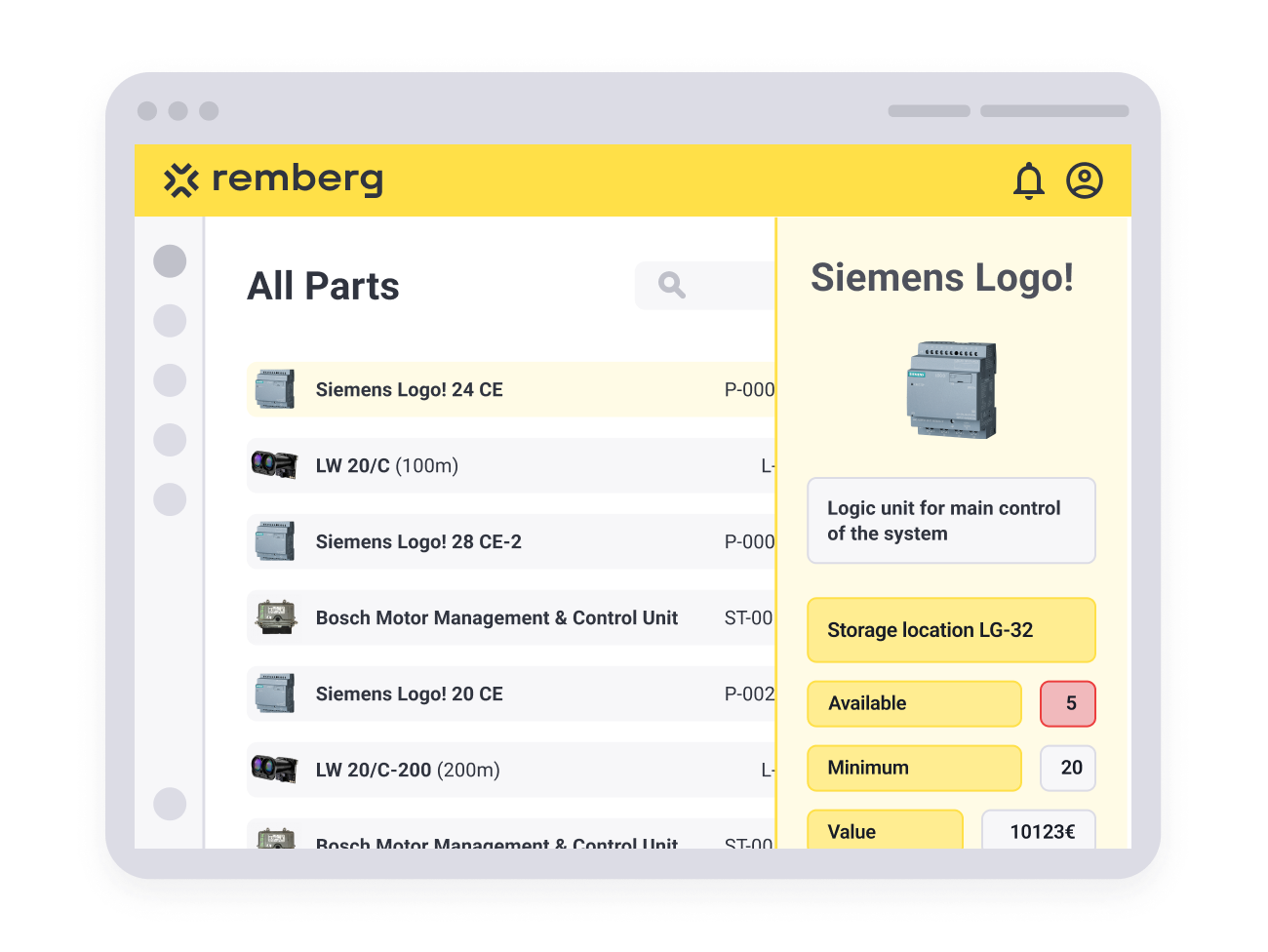
.png)
Connect your IT systems through Interfaces & APIs
remberg can be connected to all common ERP or MES systems to enable a mobile, AI-powered user experience for maintenance teams. Find out more about our documented interfaces in our remberg developer portal.
Trust in world-class data protection & IT security
Your data and your trust are our top priority. For hosting, the remberg software relies on a German high-security data center that is ISO/IEC 27001 certified and meets the highest C5 standards of the German Federal Office for Information Security (BSI). Additionally remberg provides security mechanisms such as password change cycles and 2FA.
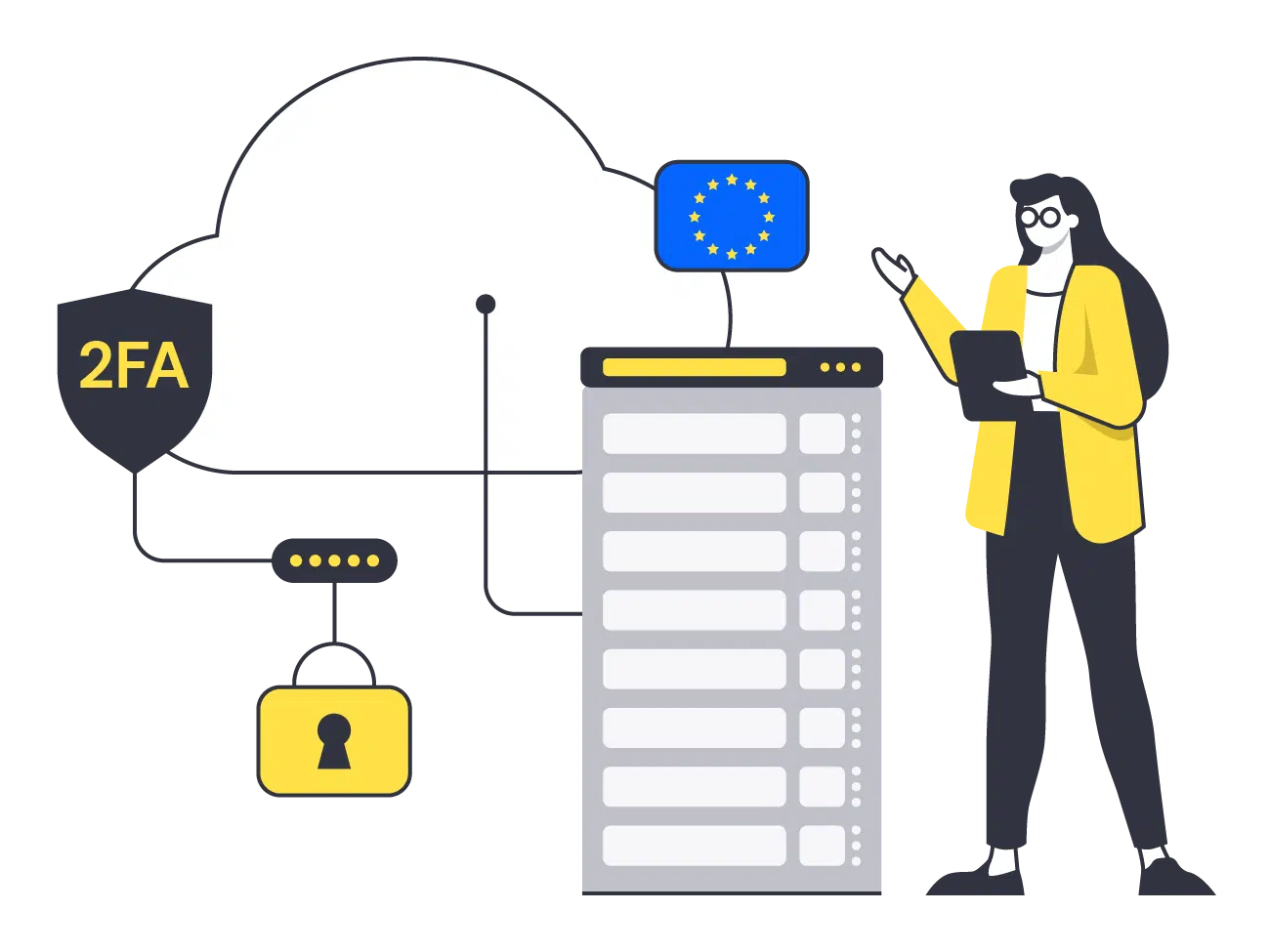
Our customers
Unlock the Full Potential of Your Assets, Equipment & Facilities
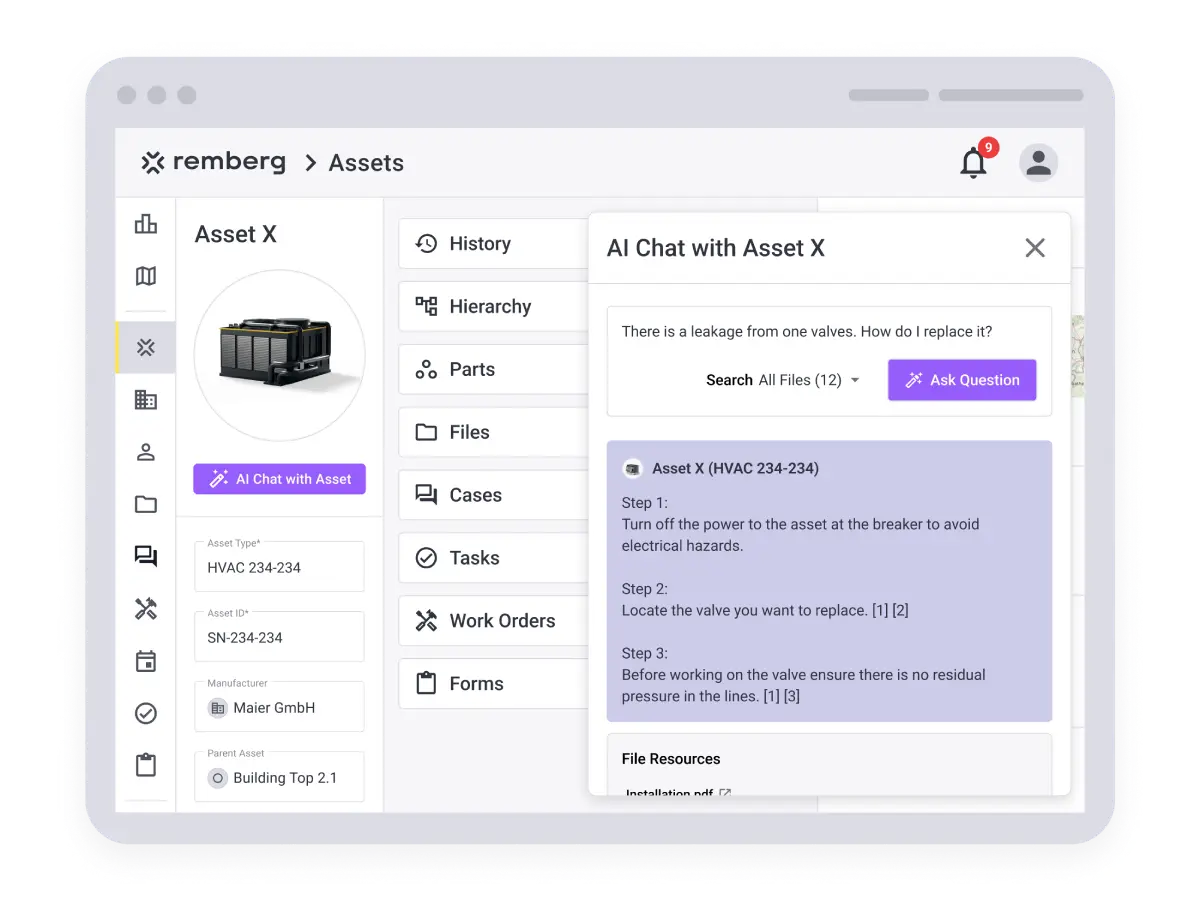
Newsletter
Inspiring content, trends & news.