Our customers
The problem
Assets stay in use for decades – but their lifecycle data around maintenance and operation is fragmented, outdated, or undocumented.
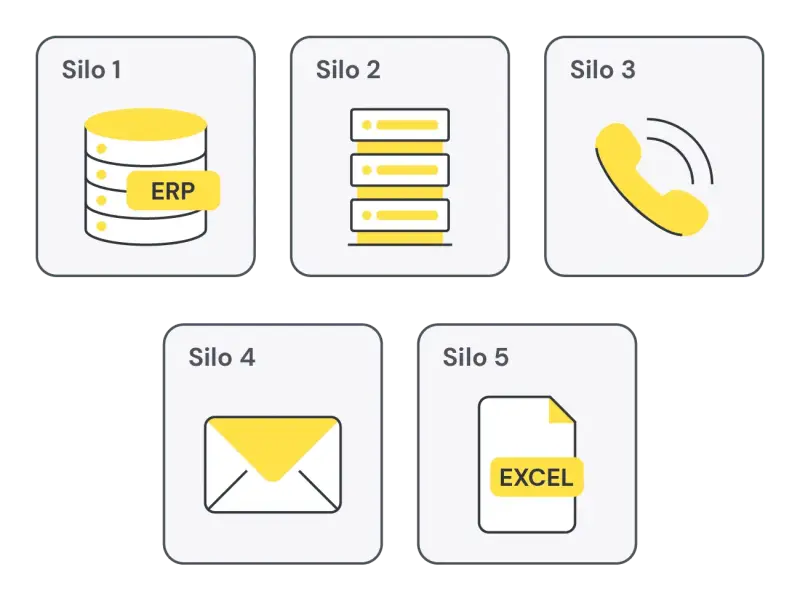
Before
- No transparency: Information is scattered across ERP systems, file servers, Excel sheets, sticky notes, and emails – making it hard to get a clear overview.
- Incomplete: Many tasks go undocumented – especially ad-hoc fixes or work done by external service providers.
- Error-prone: Data gets lost or outdated because no one knows what was done last.
- Time-consuming: Analyzing breakdowns or preparing for audits takes hours – just to gather the right info.
- Not future-ready: Paper-based workflows and Excel aren’t built for modern, AI-powered maintenance.
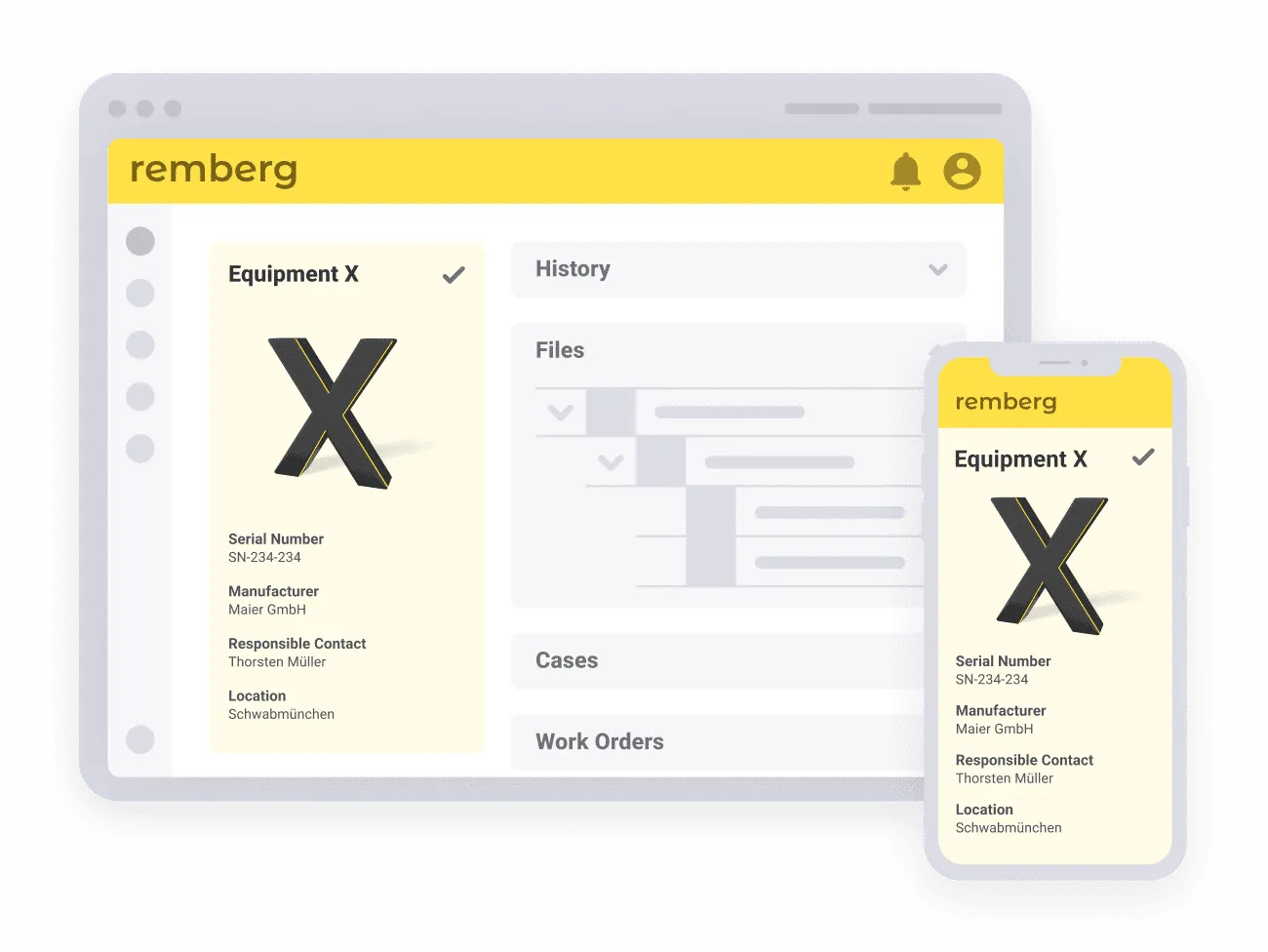
After
- Transparent: All asset info is centralized, searchable, and accessible via app or desktop – always linked to the right asset.
- Complete: Every action is logged – from maintenance and repairs to inspections and replacements, even by external partners.
- Traceable: Instantly see what was done, by whom, when, and why – with all reports, checklists, and notes in one place.
- Time-saving: Stop wasting time searching. Find everything in seconds – for audits, shift handovers, or troubleshooting.
- Future-proof: Digital workflows instead of Excel and paper – supported by the remberg AI Copilot
Build a complete digital history of your assets
With remberg, every maintenance task, incidents, and inspections are automatically recorded and linked to the right asset. Work orders, checklists, and documents all flow into one central system.
Over time, you create a searchable, audit-ready knowledge base your whole team can rely on.
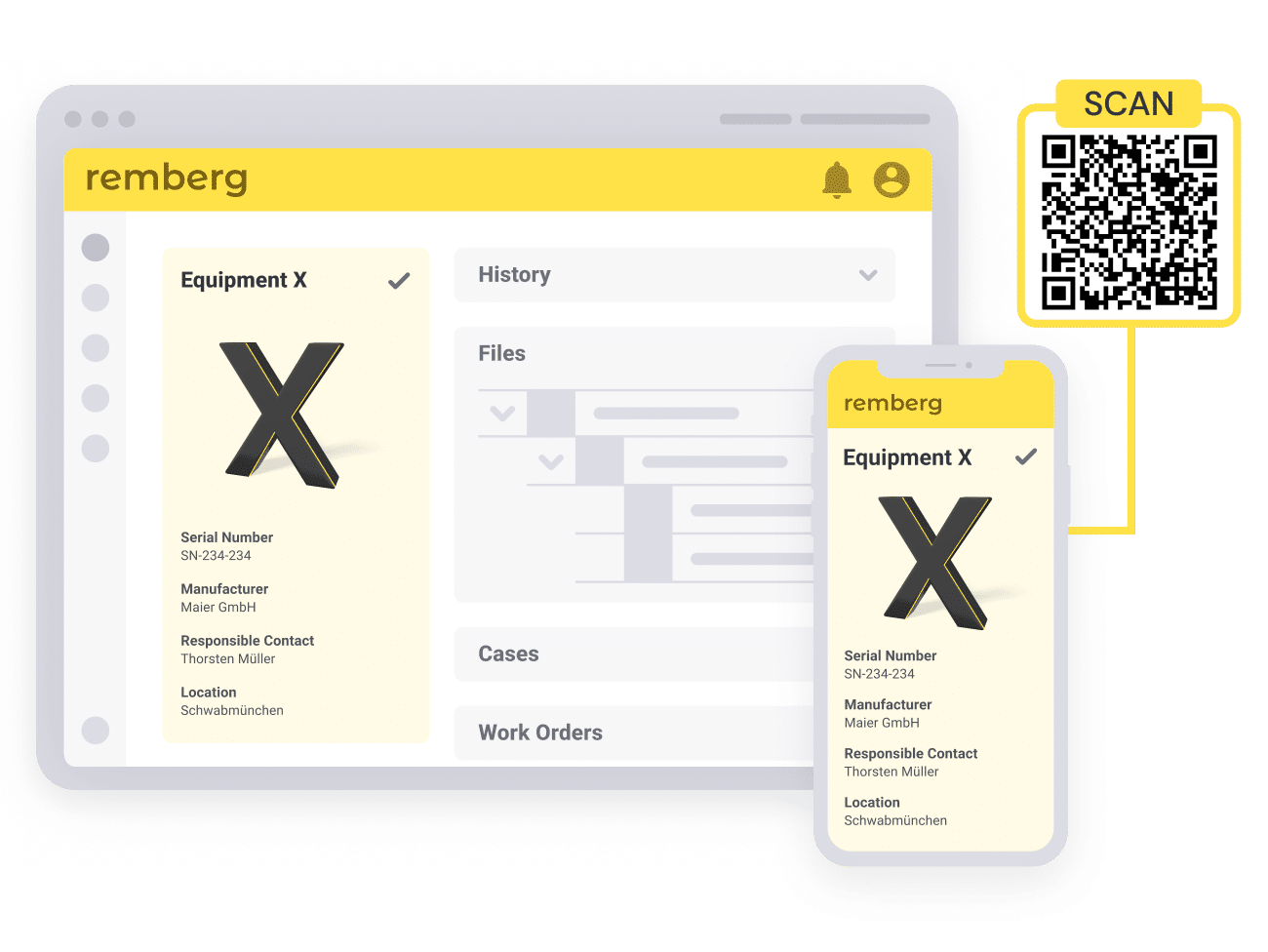
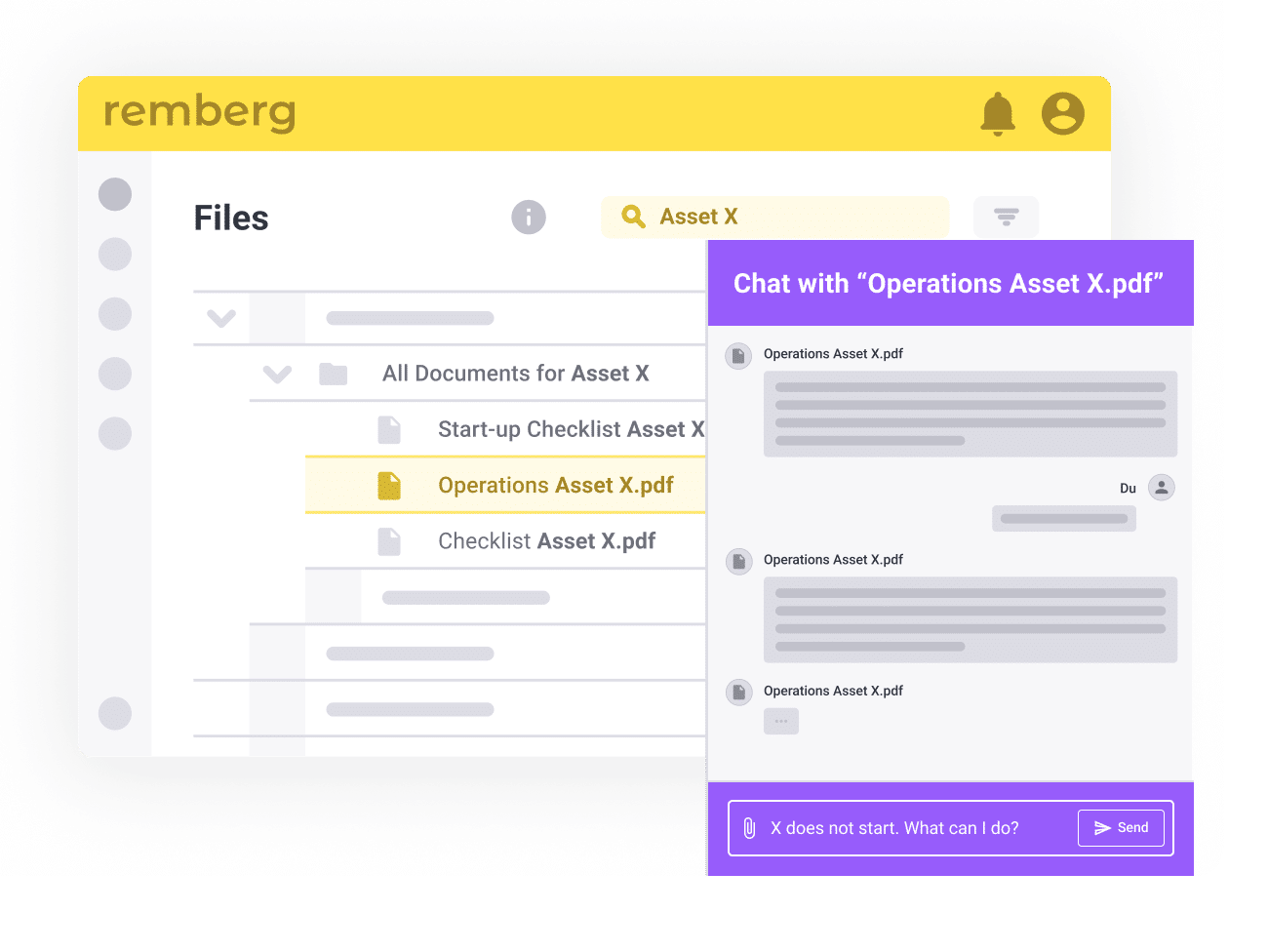
Get answers in seconds – wherever you are
Whether you're in a production site, at your desk, or right next to the machine – remberg gives you instant access to everything you need. The remberg AI Copilot scans past reports, technical docs, and asset data to deliver accurate, fact-based answers – always linked to the right asset. No delays. No guesswork. Just answers - exactly when you need them.
Sync all your data across systems
Easily connect the remberg maintenance software with your existing ERP, DMS, or PDM systems. Standardized interfaces ensure your asset data stays in sync – continuously and automatically. This creates a single source of truth, enabling more efficient processes and better, data-driven decisions.
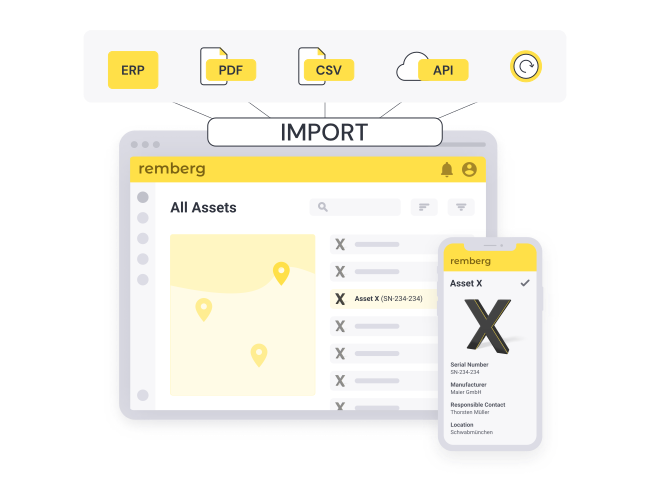
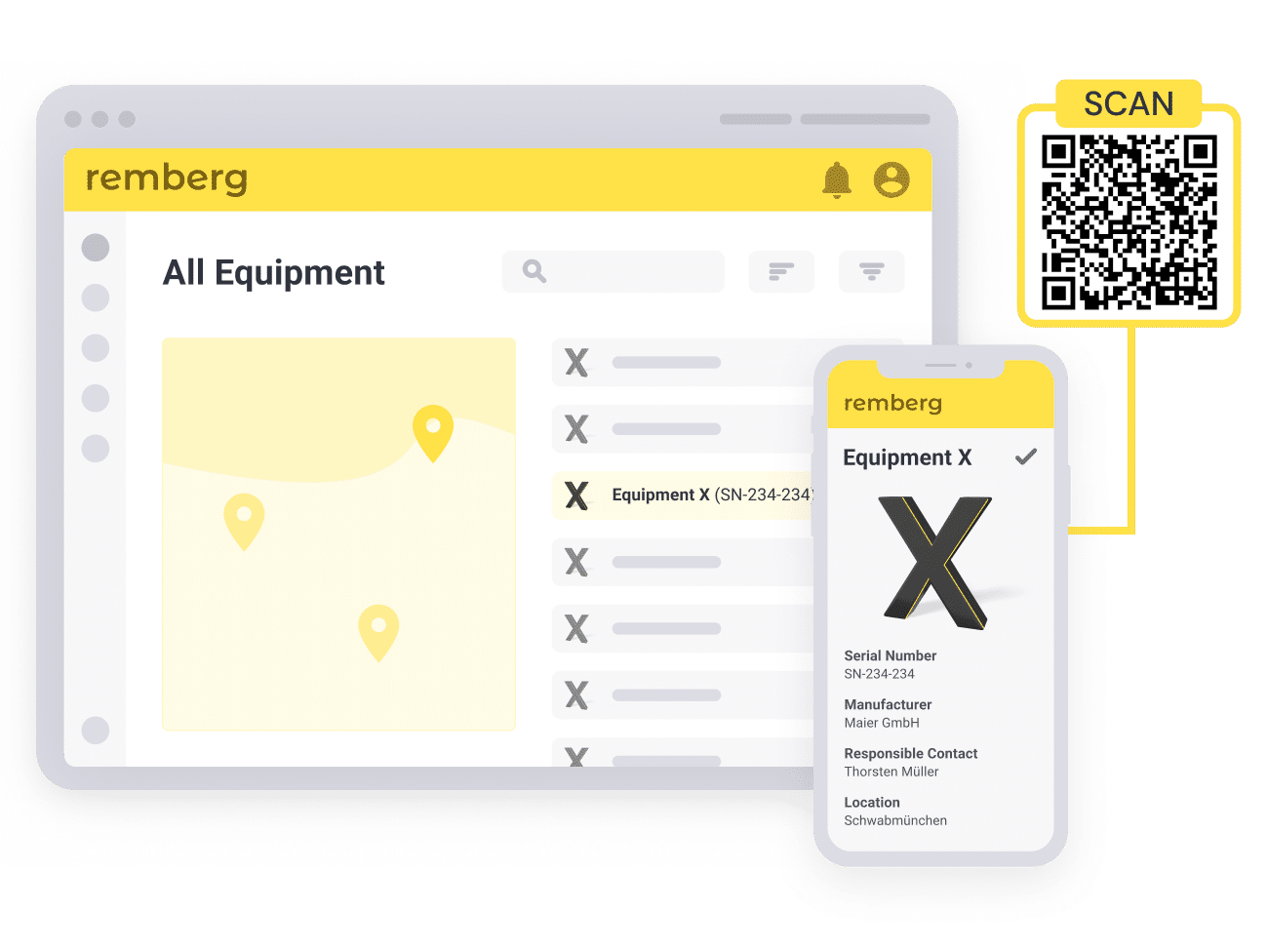
Keep critical knowledge – even when your team changes
When team members leave or retire, valuable know-how often disappears with them. With remberg, every task is documented and linked to the asset – so your team’s experience stays accessible, no matter who’s on shift.
Be audit-ready – without the stress
Maintenance audits or supplier checks can be a nightmare when documentation is missing or hard to find. With remberg, every inspection, task, and repair is fully documented – audit-proof, instantly accessible, and linked to the right asset.

.png)
Connect your IT systems through Interfaces & APIs
remberg can be connected to all common ERP or MES systems to enable a mobile, AI-powered user experience for maintenance teams. Find out more about our documented interfaces in our remberg developer portal.
Trust in world-class data protection & IT security
Your data and your trust are our top priority. For hosting, the remberg software relies on a German high-security data center that is ISO/IEC 27001 certified and meets the highest C5 standards of the German Federal Office for Information Security (BSI). Additionally remberg provides security mechanisms such as password change cycles and 2FA.
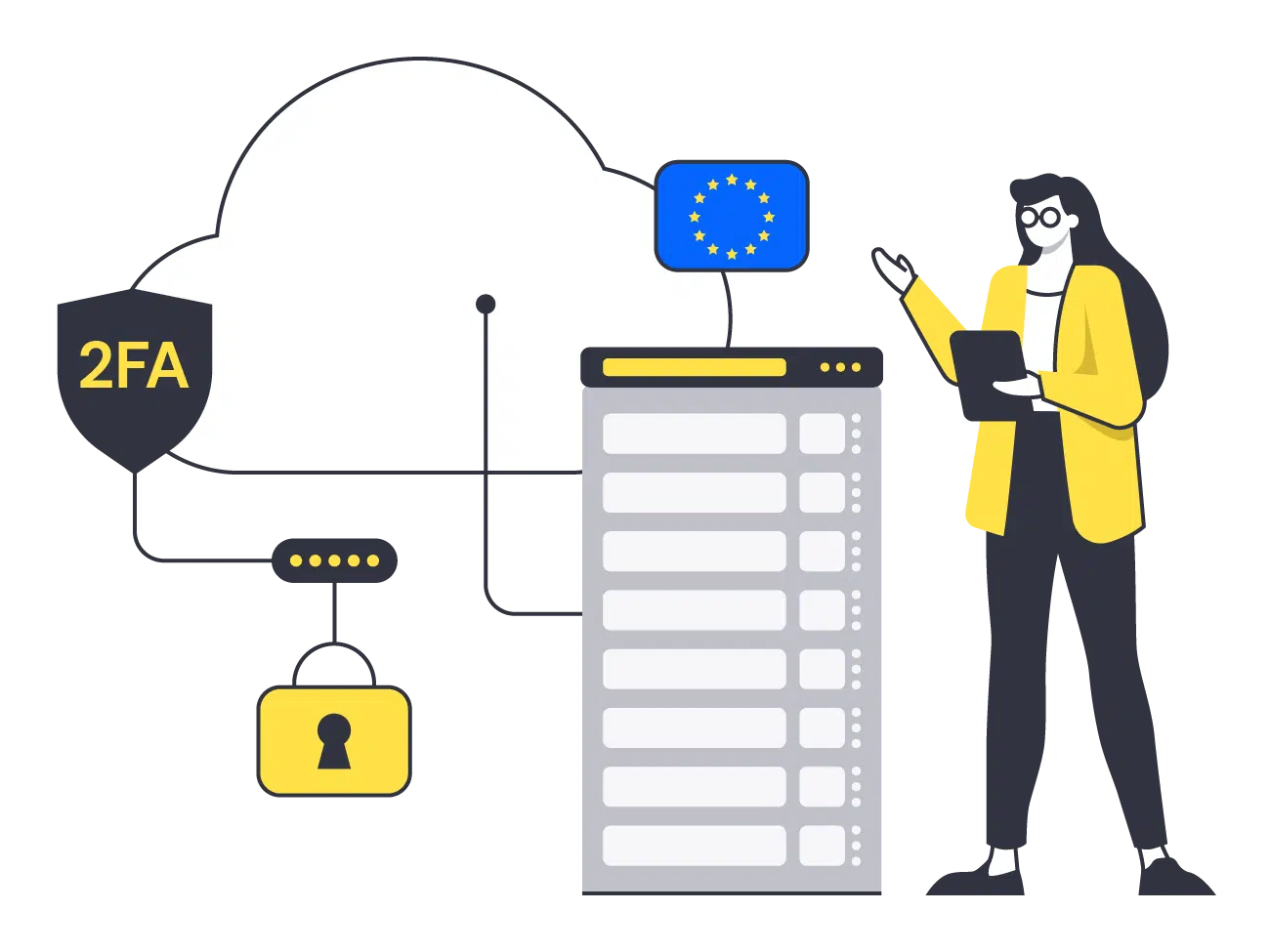
Our customers
Unlock the Full Potential of Your Assets, Equipment & Facilities
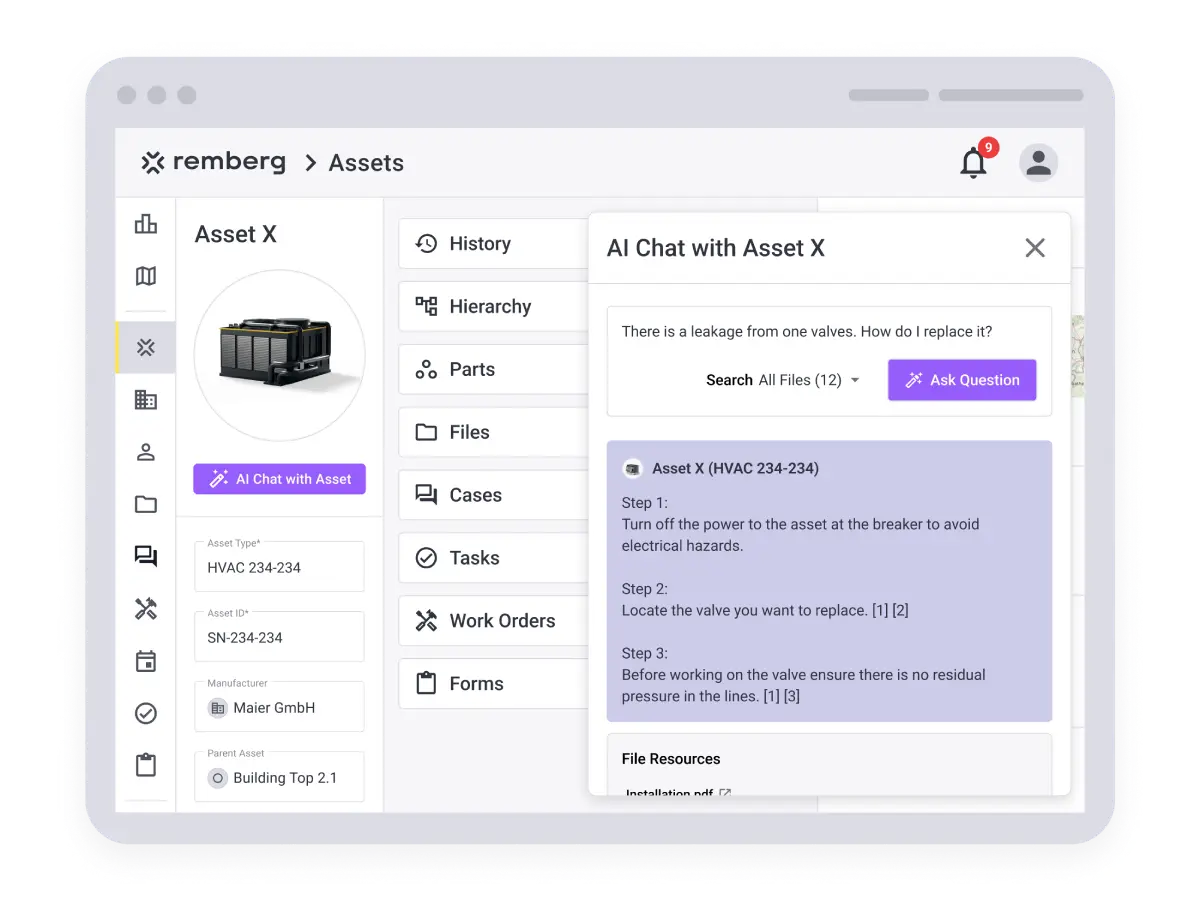
Asset Management
EU Machinery Directive and new Machinery Ordinance
EU requirements: Product safety requires maintenance documentation
The Machinery Directive 2006/42/EC and the new Machinery Regulation (EU) 2023/1230 provide the legal framework for the product safety of machinery in Europe. Both stipulate that machinery may only be operated if it is safe when properly installed and maintained. Manufacturers must already create extensive technical documentation and risk assessments for CE marking and keep them for the entire service life of a machine. The upcoming Machinery Regulation (from 2027) further tightens these requirements – especially in the area of safety, risk assessment and documentation. One of the EU's stated goals is to reduce paper-based documentation: digital documentation is intended to save monetary and ecological costs associated with paper. For maintenance personnel, this means that anyone who operates or maintains machines must consistently document the prescribed maintenance and tests (preferably digitally) in order to ensure ongoing safety and compliance.
Duty of proof: Why digitally document maintenance?
German companies have a clear obligation to provide evidence to authorities and accident insurers. For example, the German Industrial Safety Regulation (BetrSichV) requires that all initial and repeat inspections of work equipment be documented. These records must be kept for an appropriate period of time, at least until the next inspection. The German Social Accident Insurance (DGUV) also stipulates that test results must be recorded in writing – including all measured values and any defects detected. This documentation is essential to be legally protected in the event of an accident at work. In short, without complete maintenance records, there is no proof that all necessary safety measures have been taken. During inspections, authorities and auditors are increasingly demanding digital inspection reports, as they are easier to evaluate and share. If maintenance obligations are ignored or not documented, there is a risk of liability and, in the worst case, even the loss of insurance cover from the employers' liability insurance association. Digital documentation ensures that all maintenance measures can be found at any time and are protected against manipulation – a plus in legal security for the operator.
Practical benefits of modern maintenance software
In addition to fulfilling legal obligations, digital systems for maintenance and inspection documentation offer considerable practical advantages. Maintenance staff in industry benefit from:
- Seamless traceability and auditability: The structured, standardised recording of all maintenance work creates a complete history of each machine. This enables better tracking of the measures carried out – an essential aspect, especially for safety-relevant systems. Digitally stored records are quickly available and comprehensible for internal or external audits (e.g. by customers or supervisory authorities).
- Faster response to faults: If a system fails, digital maintenance logs allow technicians to immediately see which components were last checked or replaced. This speeds up troubleshooting considerably. Historical data reveals patterns and helps to identify problem areas at an early stage.
- Preventive maintenance and fewer failures: Digital maintenance data forms the basis for predictive maintenance. Regularly recorded measurement values and inspection reports make it possible to analyse wear trends and carry out maintenance before a failure occurs. This reduces unplanned downtime and extends the service life of machines.
- More efficient processes & less paperwork: Modern maintenance software replaces paperwork. Inspection reports and maintenance logs are stored centrally and are also readily available on mobile devices at all times. Additional work – such as manually transferring handwritten logs – is no longer necessary. Automatic reminders ensure that no inspection deadline is missed. Overall, digital solutions save time, reduce errors and create transparency for the entire team.
Conclusion
Digital documentation of maintenance measures is essential today to meet product safety and legal requirements. In view of the tightened requirements of the EU Machinery Directive and the new Machinery Ordinance, companies should digitise their maintenance processes now. This will keep them on the safe side with regard to authorities and customers, while also benefiting from more efficient processes – from better audit results to higher plant availability through predictive maintenance.
Newsletter
Inspiring content, trends & news.