Our customers
The Problem
Too much to do – too little time.
You lose track and can hardly keep up with maintenance.
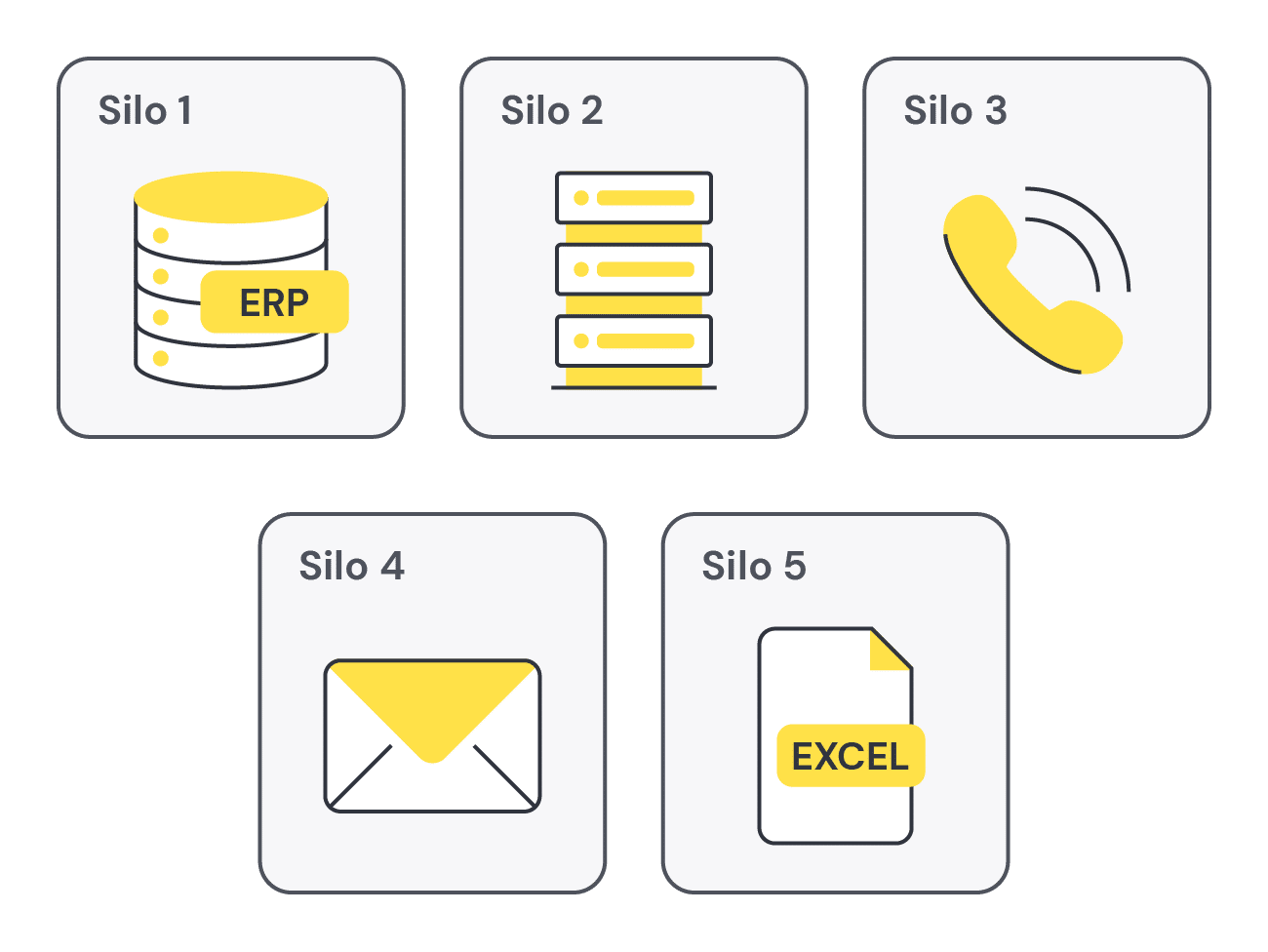
Before
- Overloaded: Too many tasks, not enough personnel. Planning falls behind, disruptions rule the day.
- Unclear: Excel, SAP, paper – but no central overview. Nobody knows what was done.
- Audits = stress: Documentation is scattered, incomplete, or duplicated – every audit is nerve-racking.
- Loss of knowledge: What happened yesterday isn’t recorded anywhere. Shift handovers happen verbally or not at all.
- Not practical: Your old software is too complicated – nobody likes using it or does it properly.
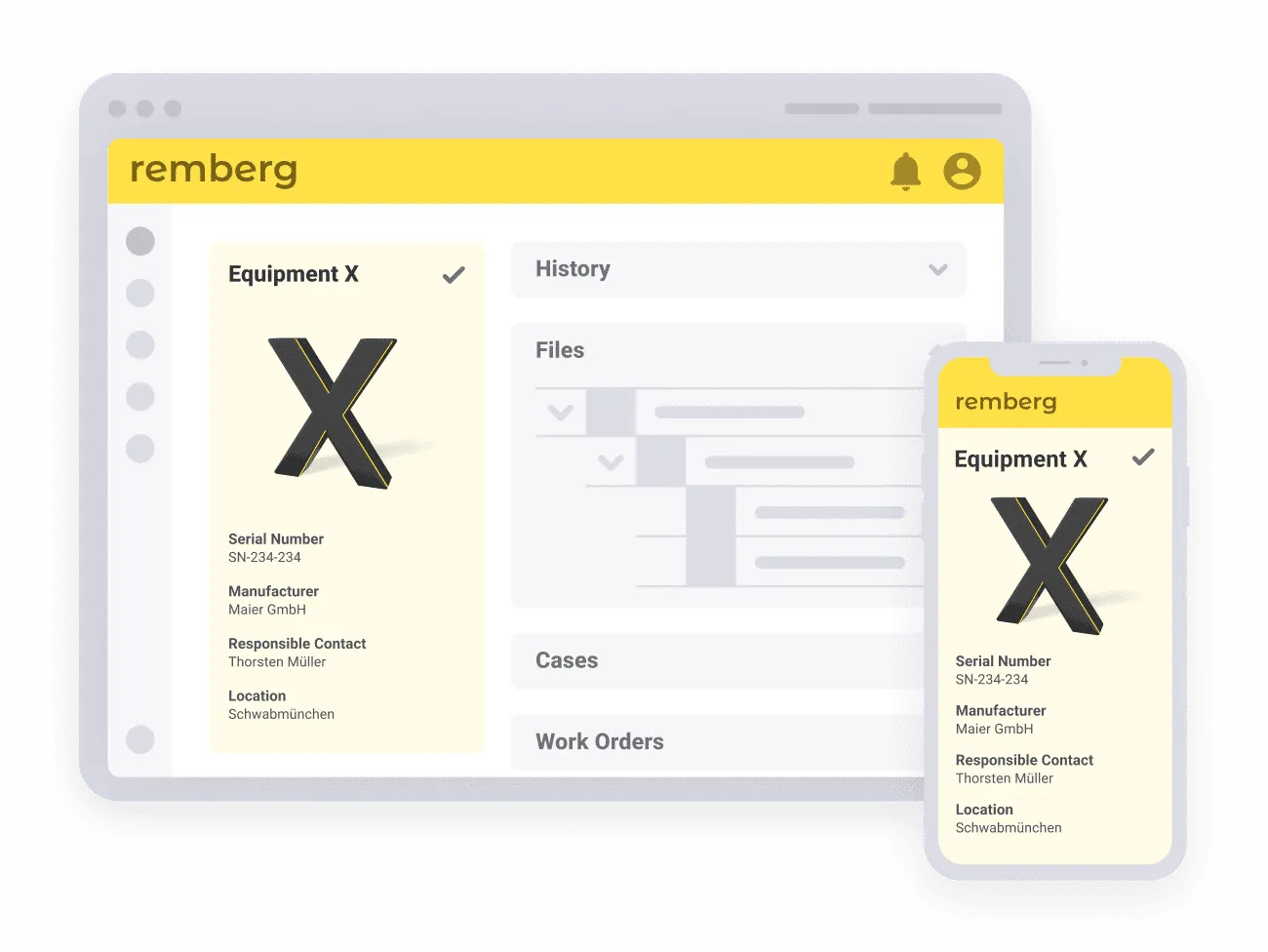
After
- Everything in one place: Assets, faults, maintenance, spare parts – clearly organized, digital, and available on the go.
- Planned: Maintenance schedules are met, tasks are assigned, priorities are always clear.
- Automated: The AI Copilot helps you troubleshoot and document.
- Knowledge stays alive: Everyone sees what got done – even the next day or in the next shift.
- Simple: remberg is intuitive. Technical teams immediately know what to do – no training, no frustration.
Keep track of everything - in one place
All the info you need – clear, up-to-date, and centralized. With remberg, you see at a glance which maintenance tasks are due, what has been completed, and where spare parts are missing. No more searching through Excel, folders, or old emails. Whether documents, technical specs, inspection reports, or notes from the last shift – everything is right where you need it. The AI Copilot even helps you resolve downtime faster and gives you the info you need immediately – no asking around, no waiting.
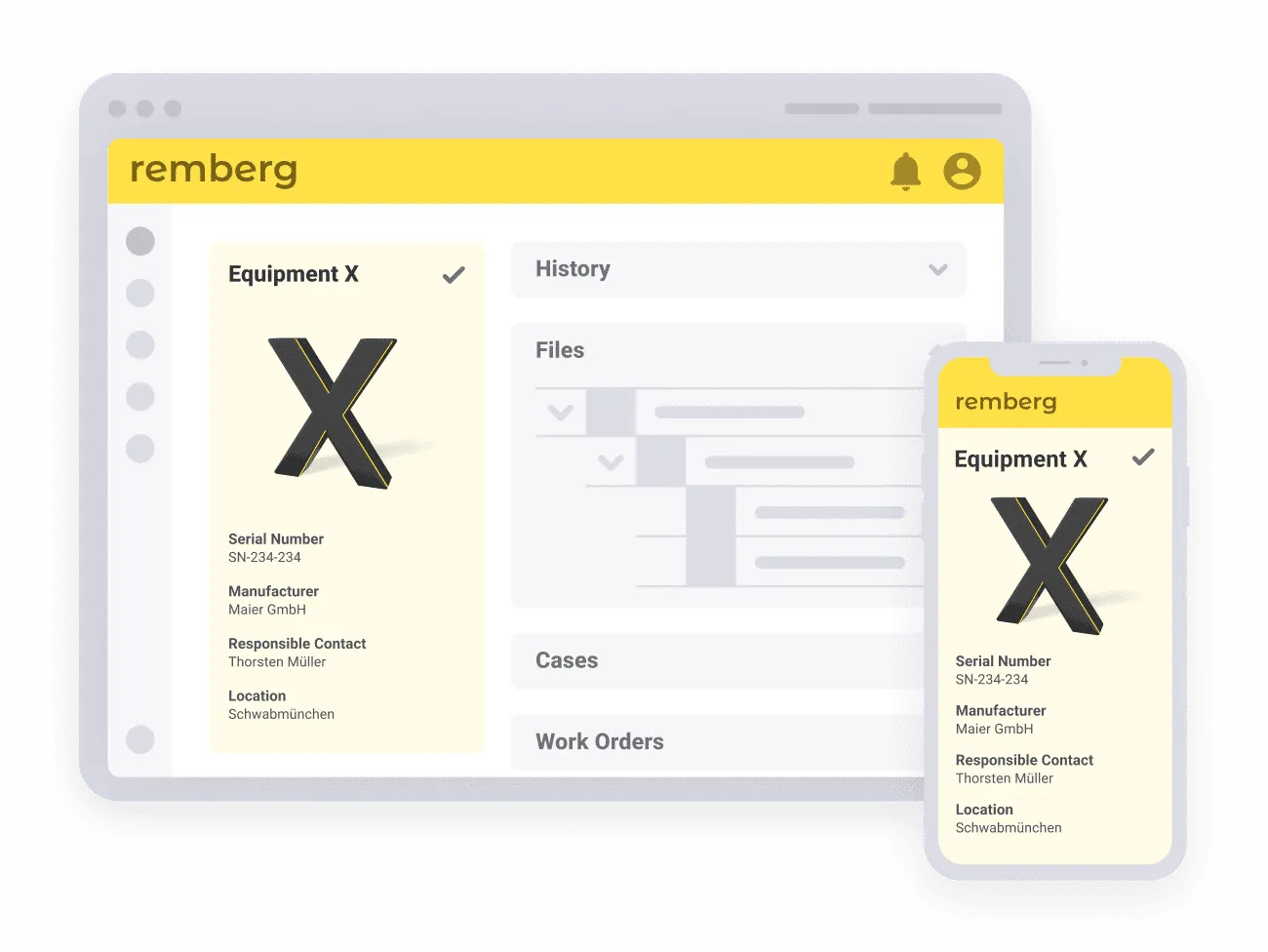
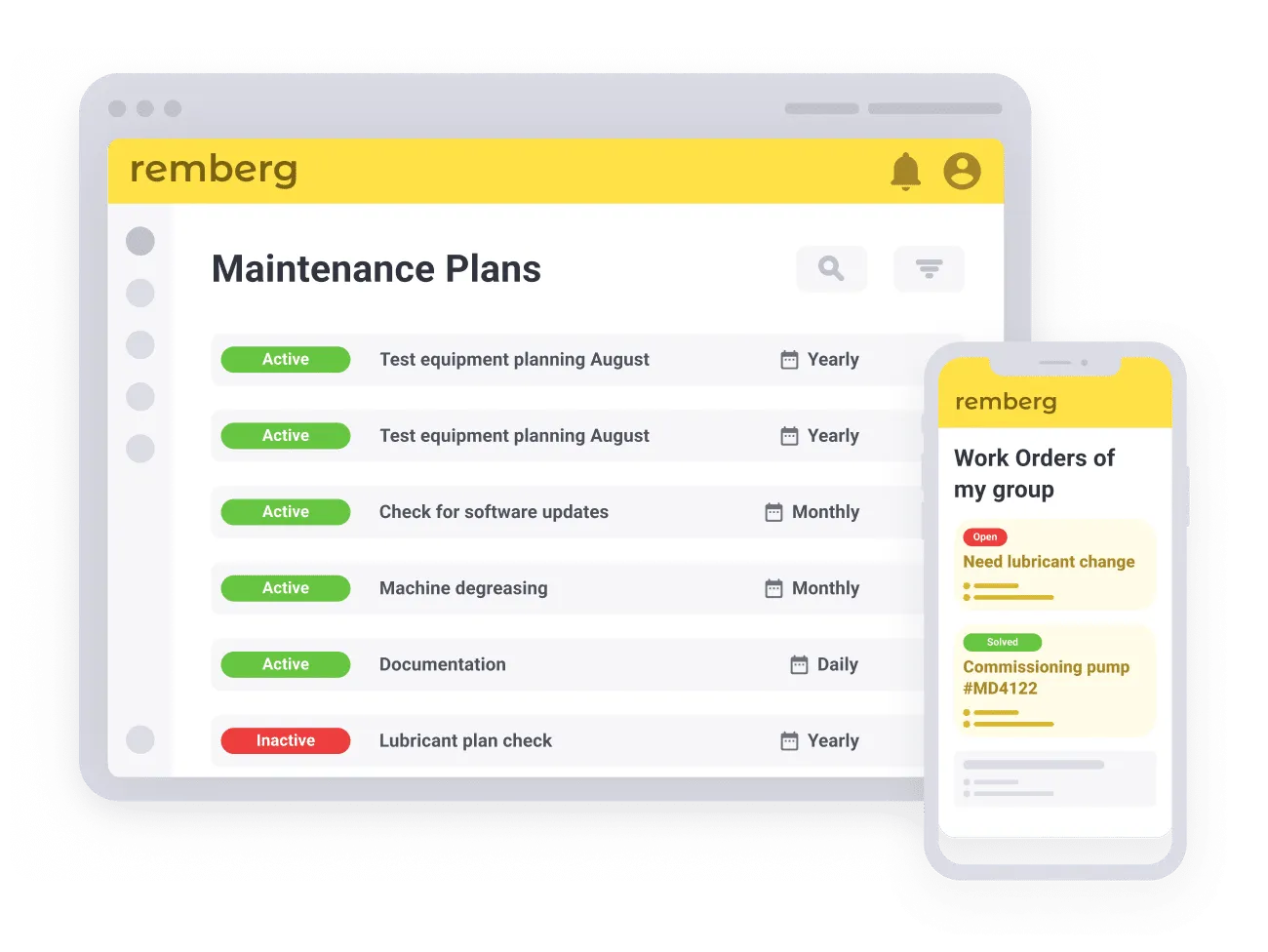
Avoid downtime with preventive maintenance
With remberg, preventive maintenance finally becomes a reality. You always know what is scheduled, what is done - and what isn't. All information is recorded digitally, so proof for audits is never a hassle. Instead of juggling Excel and paper, you use a single solution that is mobile, easy, and audit-proof. It keeps your team efficient and organized-even during busy times.
Digitize Forms and Checklists
With remberg, you can digitize inspection and maintenance checklists, inspections and much more - mobile, offline-capable, audit-proof and tailored to your use case. The forms are easy to fill out and automatically saved in the system. Photos, required fields, comments, and digital signatures ensure that nothing is overlooked. Save up to 25% on administrative work and stay audit compliant at all times - no paper, no rework.

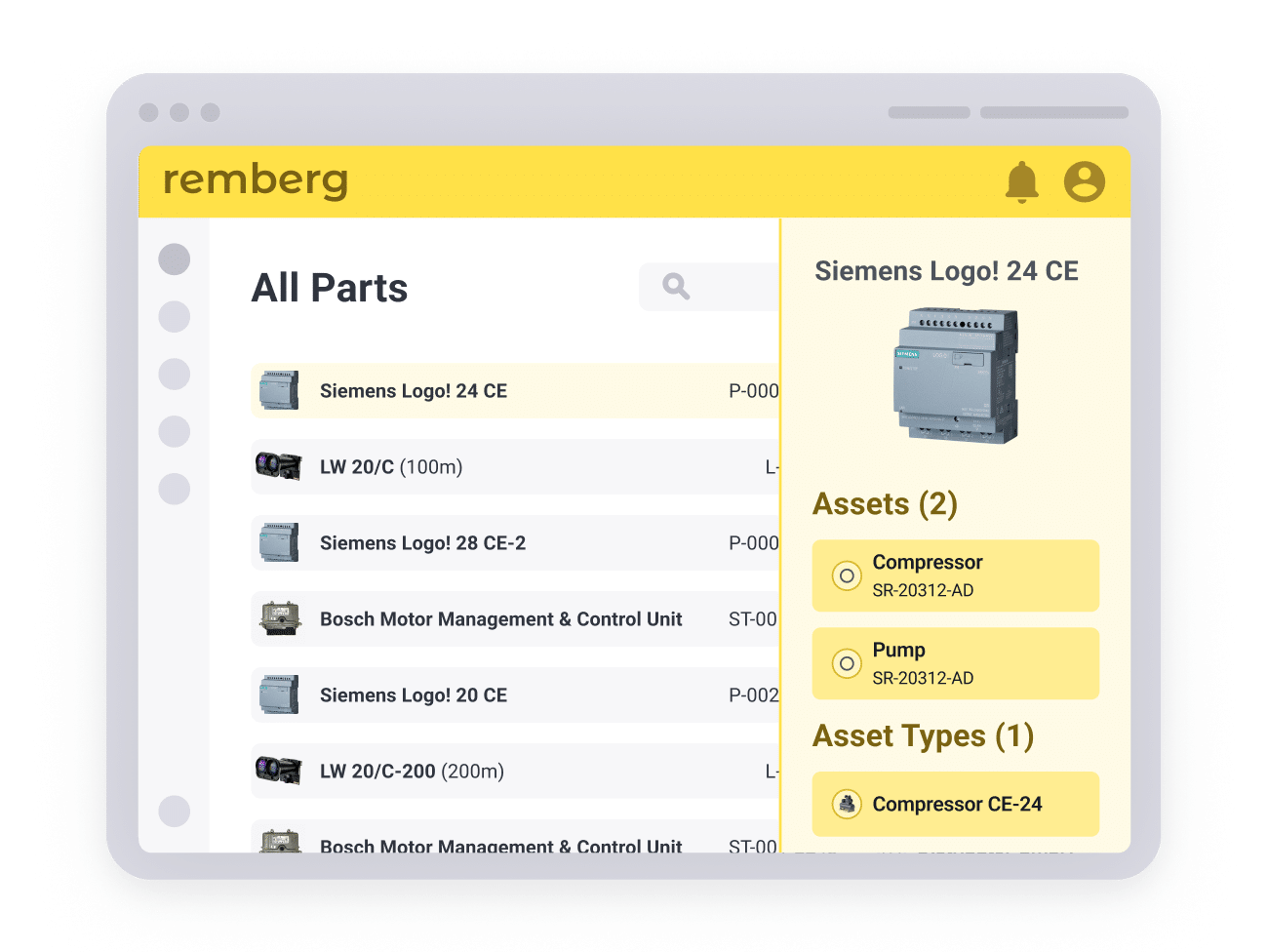
Find spare parts instead of searching for them
With the parts and inventory management in the remberg CMMS, you finally know what parts are available - and where they are located. All parts are centrally documented, complete with location, inventory, and linked to the asset. Your technical teams can find what they need instantly, right from a tablet or smartphone - no more piles of paper, no more searching. They can see what's missing, what's installed, and what needs to be reordered. This reduces downtime, eliminates duplicate inventory, and saves money.
Augment your maintenance teams with AI
The remberg AI Copilot gives you exactly the information you need to keep operations running. Whether it's circuit diagrams or an answer that is buried in your technical documentation - you'll find anything up to 10x faster, without endless searching. Create maintenance logs and documentation at the touch of a button. You save time, stay organized, and focus on what really matters: keeping your assets up and running.
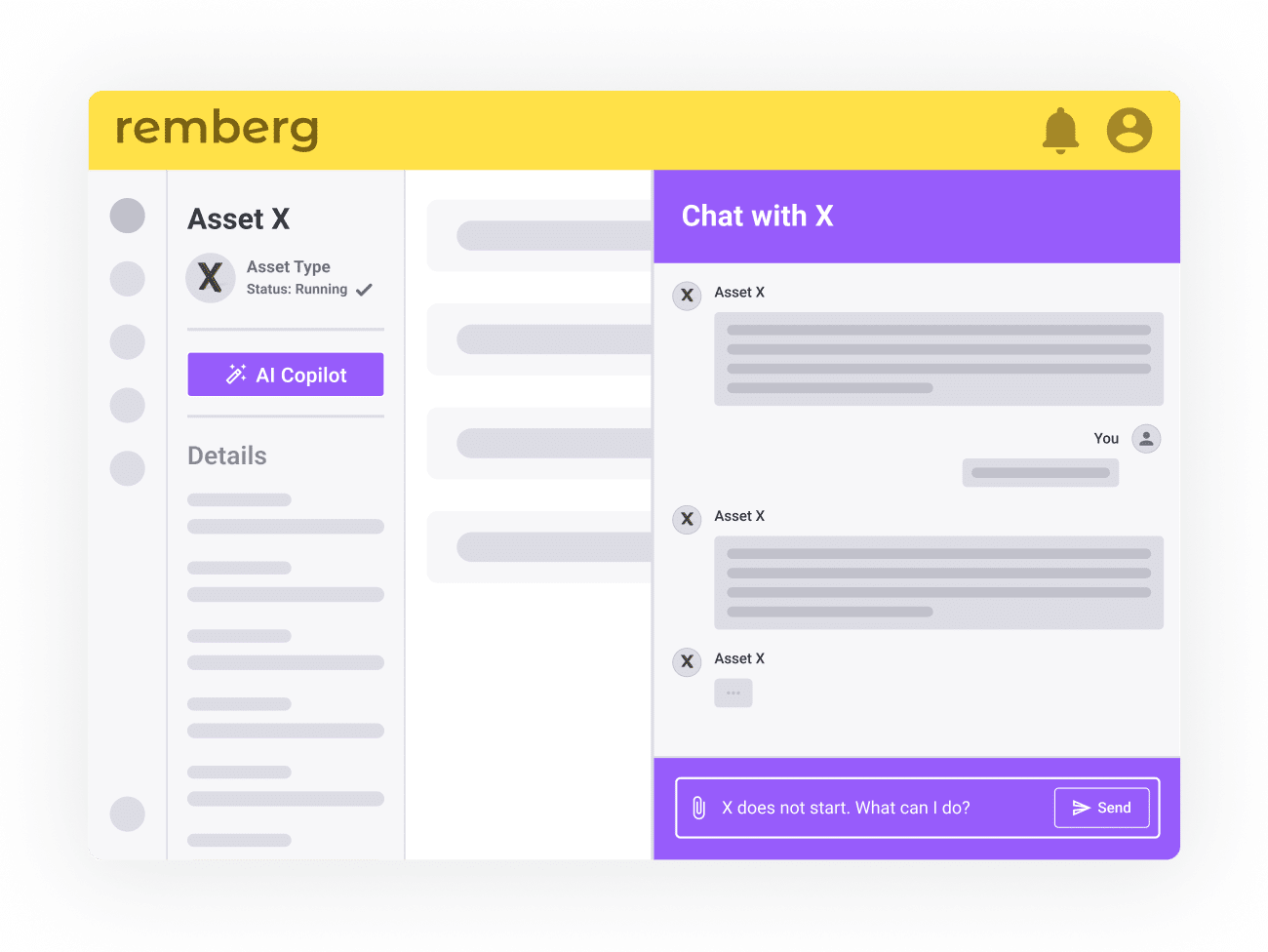
.png)
Connect your IT systems through Interfaces & APIs
remberg can be connected to all common ERP or MES systems to enable a mobile, AI-powered user experience for maintenance teams. Find out more about our documented interfaces in our remberg developer portal.
Trust in world-class data protection & IT security
Your data and your trust are our top priority. For hosting, the remberg software relies on a German high-security data center that is ISO/IEC 27001 certified and meets the highest C5 standards of the German Federal Office for Information Security (BSI). Additionally remberg provides security mechanisms such as password change cycles and 2FA.
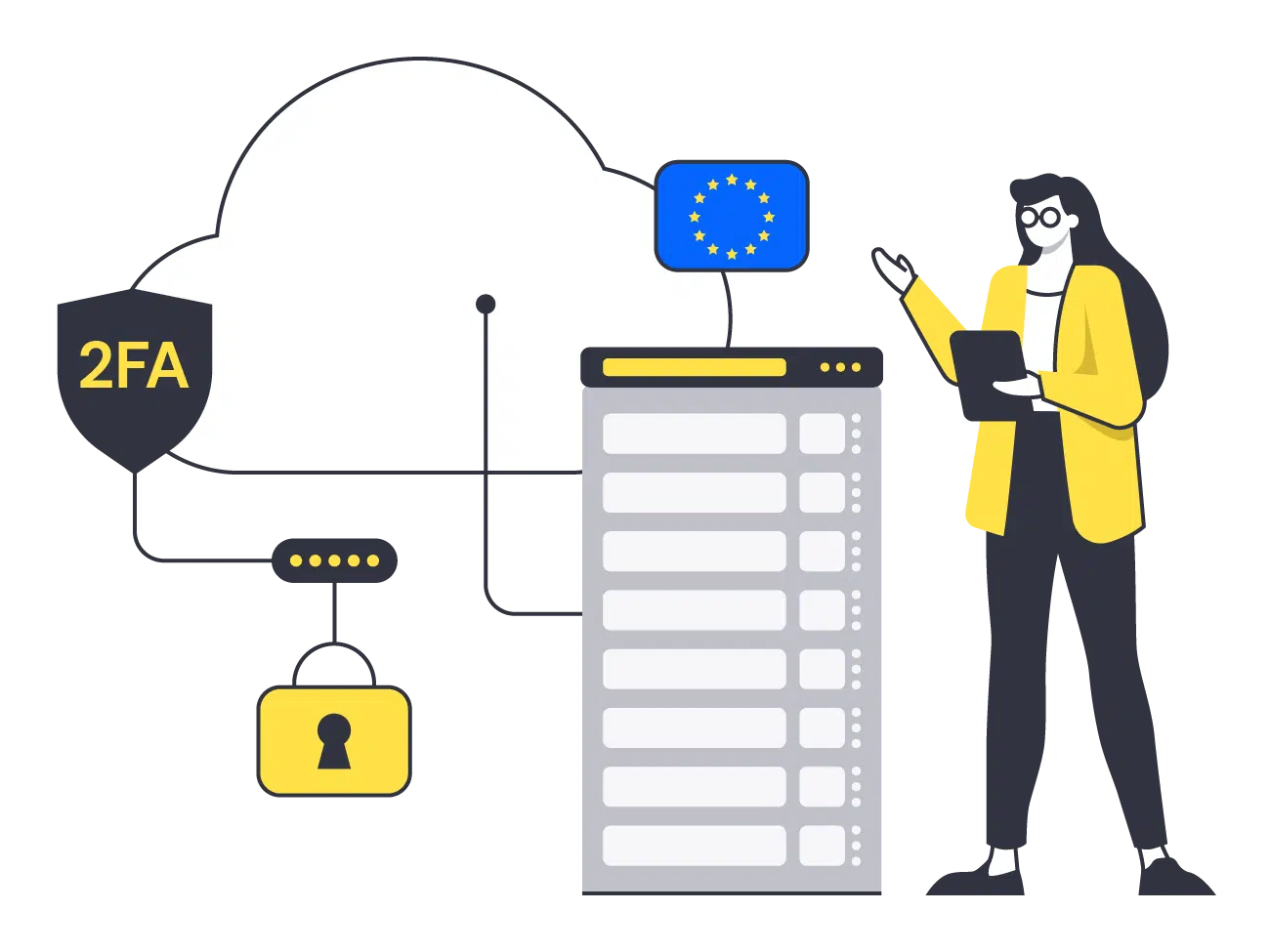
See how our customers use the Intelligent Maintenance Software
Get rid of unplanned downtime with the Intelligent Maintenance Software
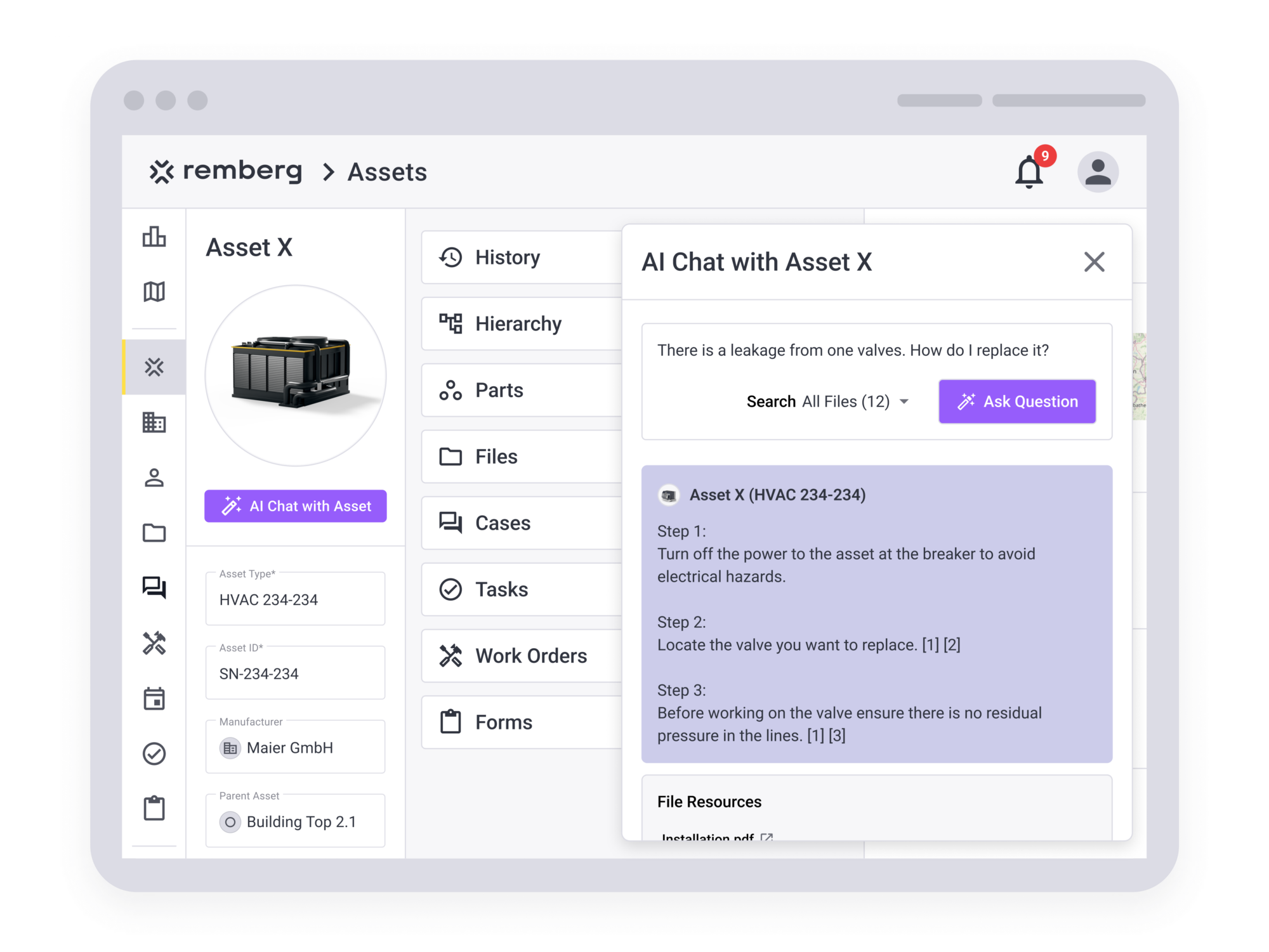
remberg, the Intelligent Maintenance Software
Digitize maintenance, repair and operations
Why digital maintenance is indispensable
Maintenance saves costs
Those who regularly check and maintain their machines and systems avoid expensive emergency repairs and unforeseen breakdowns. Instead of having to replace entire systems, small interventions are often enough to keep production running smoothly. Digital tools help to identify maintenance needs at an early stage and order spare parts in good time.
Maintenance makes everything more sustainable
Scheduled maintenance extends the service life of assets and components, which reduces the consumption of resources. By maintaining and repairing existing systems instead of constantly purchasing new machines, the ecological footprint is also reduced.
Maintenance is long-term and strategic
A well-thought-out maintenance strategy protects against surprises. Those who only react to faults waste time, money and nerves. Digital maintenance systems provide reliable information on the condition of assets, so that maintenance intervals can be better planned. This increases availability – and the company can concentrate on the essentials.
Maintenance needs all-rounders
Modern maintenance is anything but monotonous screwdriving. Specialists must be able to evaluate sensor values, optimize processes and react flexibly to new technologies. Digital platforms support these skills by networking knowledge and facilitating the exchange of information between technology, IT and management.
Maintenance increases safety and quality
When machines are running optimally and are regularly inspected, the risk of accidents and quality defects is reduced. Digital protocols record all maintenance activities and facilitate audits and certifications. This not only increases confidence in one's own products, but also customer satisfaction.
Maintenance with remberg
Key digital maintenance features that make a difference
Pens, paper, Excel lists or desktop software have served us well, but let's face it: it's usually quite cumbersome.
As a maintenance professional, you are responsible for keeping assets running efficiently, minimizing downtime and optimizing maintenance processes. The following modular features give you exactly the tools you need for your daily work:
- Asset Management: Get complete transparency over every single asset and its condition, so you always know exactly when and where action is needed.
- Work Order Management: Plan and track your repairs, maintenance, and inspections centrally to assign tasks faster and seamlessly document their processing.
- Parts & InventoryAlways keep track of your spare parts inventory and link relevant components directly to your assets to avoid unnecessary downtime.
- Preventive maintenance: Plan recurring maintenance tasks with automatic reminders so that you can proactively avoid downtime and increase the service life of your equipment.
- AI Copilot: The AI Copilot complements your team and provides support in various functions, such as troubleshooting or documentation. This enables you to solve problems faster and save your team valuable time.
- Facility Management: Coordinate reports, rooms and service providers centrally so that you can efficiently control all measures related to buildings and infrastructure.
- Planning & resources: Assign maintenance and repair orders to your team or specific machines using drag and drop and avoid scheduling and resource conflicts.
- Partners, Suppliers & Portal: Smoothly integrate external service providers and suppliers into your maintenance processes to easily coordinate information, orders and progress.
- Dashboard & Analytics: Get centralized insights into all relevant key figures and use them to make data-driven decisions for your maintenance strategy.
- Checklists & Procedures: Create and edit maintenance logs, inspection checklists or safety documents digitally - on the go and with automatic documentation.
With these modular features, you are perfectly positioned to keep an eye on all your tasks, leverage efficiency potential and take care of your assets in the best possible way.
Would you like to test the remberg CMMS software for free in a demo? We look forward to hearing from you!
Maintenance software in the cloud
Maintenance management should be in the cloud
Are you considering moving your maintenance management software to the cloud? Good decision!
Here are some strong arguments in favor of taking this step:
First, cloud technology enables access from any location: technicians, field staff and decision-makers can access relevant data anytime and from any device. This promotes seamless collaboration and accelerates the exchange of information, which in turn significantly optimizes the maintenance process.
Secondly, the cloud offers scalability and flexibility. Companies can easily adjust their storage and functionality needs without having to make large investments in their own server structures. This makes it easier to deal with growing data volumes and increasing requirements.
Another advantage is the real-time data update. Current status messages, maintenance intervals and inventory overviews are immediately synchronized so that informed decisions can be made quickly. This makes it possible to plan and carry out repairs and deal with unforeseen problems more efficiently.
Last but not least, companies benefit from automated updates and enhanced data security: software providers ensure regular updates and patches, which reduces the need for internal IT resources. What's more, modern cloud solutions are equipped with robust security mechanisms that protect against data loss and misuse.
Thanks to these advantages, cloud-based maintenance software can help to streamline processes, increase efficiency and secure long-term competitive advantages.
Moving your CMMS software to the cloud increases your efficiency, reduces costs and increases flexibility. Do you still have concerns about cloud software? Then we have this e-book for you, in which we discuss further reasons why remberg is only available in the cloud. Furthermore, we are happy to provide you with advice – we will then work with you to see whether an implementation makes sense.
Audit-compliant maintenance
Audit-compliant maintenance documentation
How much time do you spend properly documenting your maintenance?
Your maintenance technicians use different of forms, reports and checklists to log their work. All of them are filled out differently and are stored in different filing systems, Excel lists or on paper. It's easy to get lost in a paper chaos – not to mention the stress when an audit is pending and all eyes are on maintenance.
- Maintenance reports (DIN EN 13306): Maintenance reports are essential for documenting the work carried out. They contain detailed information about the tasks performed, including parts replaced, materials used and labor time.
- Maintenance checklists (DIN 31051): Various standards such as DIN 31051 provide guidelines for creating maintenance checklists. These lists ensure that no critical maintenance steps are overlooked and are considered an absolute basis for systematic inspections.
- Inspection reports (DIN EN ISO 9001, DGUV V3): Are your inspection reports legally compliant, or are you on thin ice? Inspection reports are particularly important for companies that are ISO 9001 certified. They document all tests, inspections and reviews that have been carried out on systems or devices to ensure quality and compliance.
- Spare parts requests (DIN 4000): You can design spare parts request forms according to DIN 4000 to document and facilitate the procurement and replacement of parts.
- Safety inspections and protocols (DIN ISO 45001): DIN ISO 45001 provides guidelines for safety documentation to ensure that safety standards are met during maintenance work and that accidents at work are avoided.
- Calibration protocols (ISO 9001:2015): When it comes to technical measurements, calibration protocols and acceptance reports are important to ensure the accuracy of your measuring instruments. Calibration standards are based on strict guidelines that ensure the functionality and quality of your equipment.
- Environmental impact reports: If you work in areas with environmental impacts, you may need to prepare reports in accordance with the requirements of environmental protection laws.
- Industry-specific requirements:
- Facility management: Various operator obligations
- Food industry: IFS Version 7, DIN EN ISO 22000 – 2018-09, HACCP
- Automotive industry, e.g. ITAF 16949
- Energy plants & systems: Inspection of e-charging stations according to the current DIN VDE 0105-100 standard
With remberg, the Intelligent Maintenance Software, you digitize all relevant forms, reports and checklists, ensure that your teams always complete them correctly and be prepared for any inspection or audit.
Newsletter
Inspiring content, trends & news.