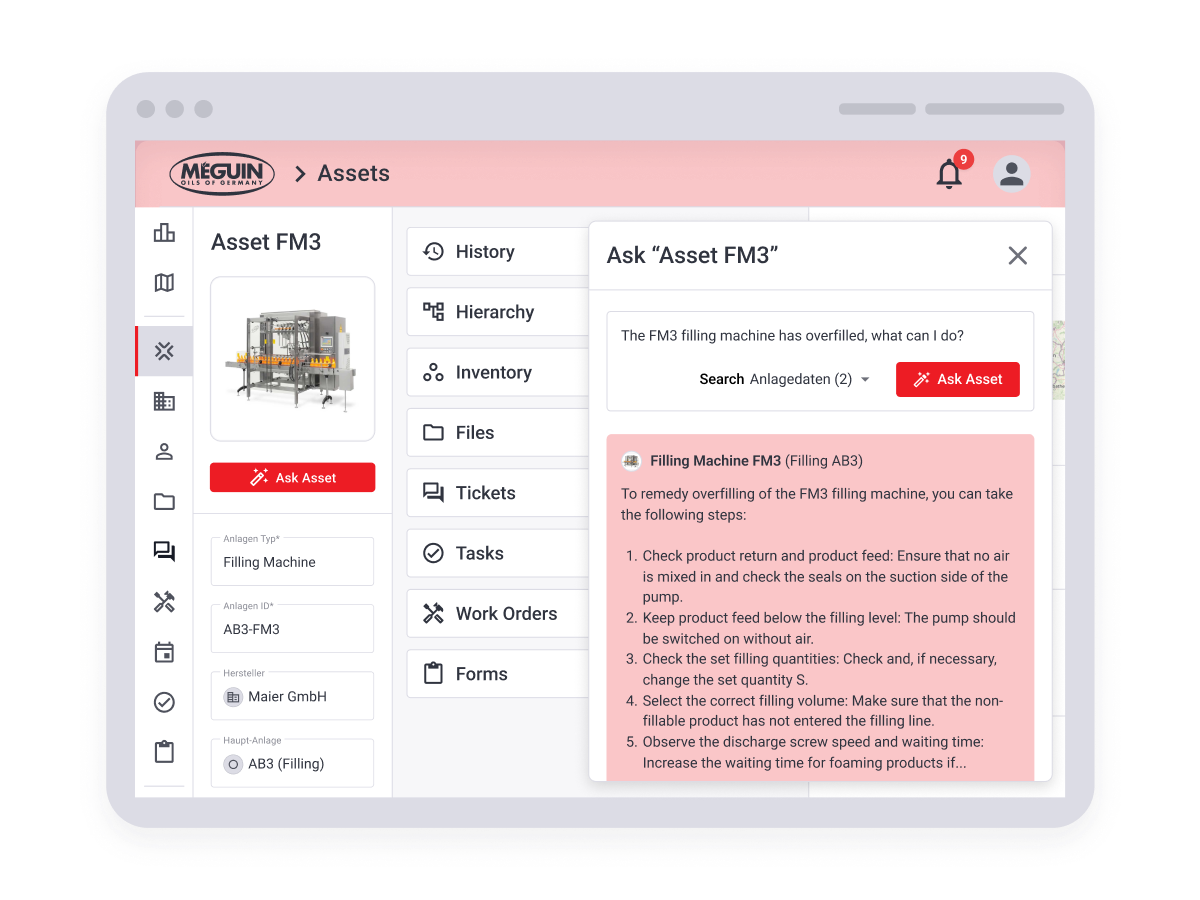
From firefighting to planned maintenance
When Christian Texter took over as Plant Manager at Meguin in 2022, his maintenance team was mainly one thing: reactive. “Back then we had ‘firefighting’ or breakdown maintenance – we only reacted when something was already broken,” says Christian Texter.
Three shifts were running at full capacity, even Saturdays were used to fix urgent issues. Downtime didn’t just cost money – it drained motivation. Documents were buried in binders, maintenance plans scattered across endless Excel sheets, spare parts “hidden” somewhere in the warehouse.
Texter recalls: “Maintenance was overloaded and too sluggish. We needed to steer the workload.”
Trying to map the processes into the existing ERP system failed quickly. As Texter puts it: “An ERP system is not a maintenance system – it’s way too slow and clunky.”
The search for a better solution
Christian Texter and his deputy head of maintenance, Patrick Längler, wanted a tool that shows all technical assets and machines in one place, reminds automatically of upcoming maintenance, works via app on the go, and goes live in weeks instead of years.
After a short proof of concept, they chose the remberg maintenance software.
Digitization? Yes, but step by step!
Meguin deliberately rolled out the digitization of maintenance with remberg in stages. The goal: to ensure the team could manage the transition smoothly without interrupting production.
Phase 1: Asset master data and QR codes
It all started with a data clean-up. All machine and asset data was exported from the ERP, standardized, and imported into remberg. Each asset then received a QR sticker. This laid the foundation for providing audit documents like maintenance reports with a single click – a huge advantage for supplier audits in over 150 export countries. Within just a few days, shift workers could scan and instantly access digital asset data, circuit diagrams, and checklists – all without disrupting operations.
Phase 2: Tickets, maintenance plans, and scheduling board
Next, the reactive maintenance process was reworked – moving from verbal reports to a structured, meaningful ticketing system. Preventive maintenance with recurring work orders was set up as maintenance plans and clearly scheduled using the scheduling board. The result: issues are logged in the system within seconds, and maintenance is planned. Personnel and spare part bottlenecks are avoided, ultimately increasing asset availability.
Phase 3: Spare parts management
In just a few weeks, the team inventoried around 4,000 spare parts and assigned storage locations. Each part was linked to its machine. Now only the relevant part appears in tickets or orders. The responsible storekeeper is automatically notified when minimum stock levels are low. Search time and capital tied up in inventory dropped dramatically.
Phase 4: AI Copilot for maintenance
On top of this clean data foundation came the highlight: the remberg AI Copilot as a digital assistant in maintenance. Whether it's an unknown error message or a maintenance task – the AI Copilot delivers clear step-by-step instructions based on the machine's technical documentation. Instead of flipping through manuals for minutes, the answer to a specific question appears in seconds and links directly to the relevant PDF page. Christian Texter is thrilled: “Document searches used to take 15 minutes in maintenance – now it’s 15 seconds.”
Thanks to this step-by-step approach, the digital maturity of Meguin’s maintenance steadily increased – without overwhelming the team or interrupting daily production.
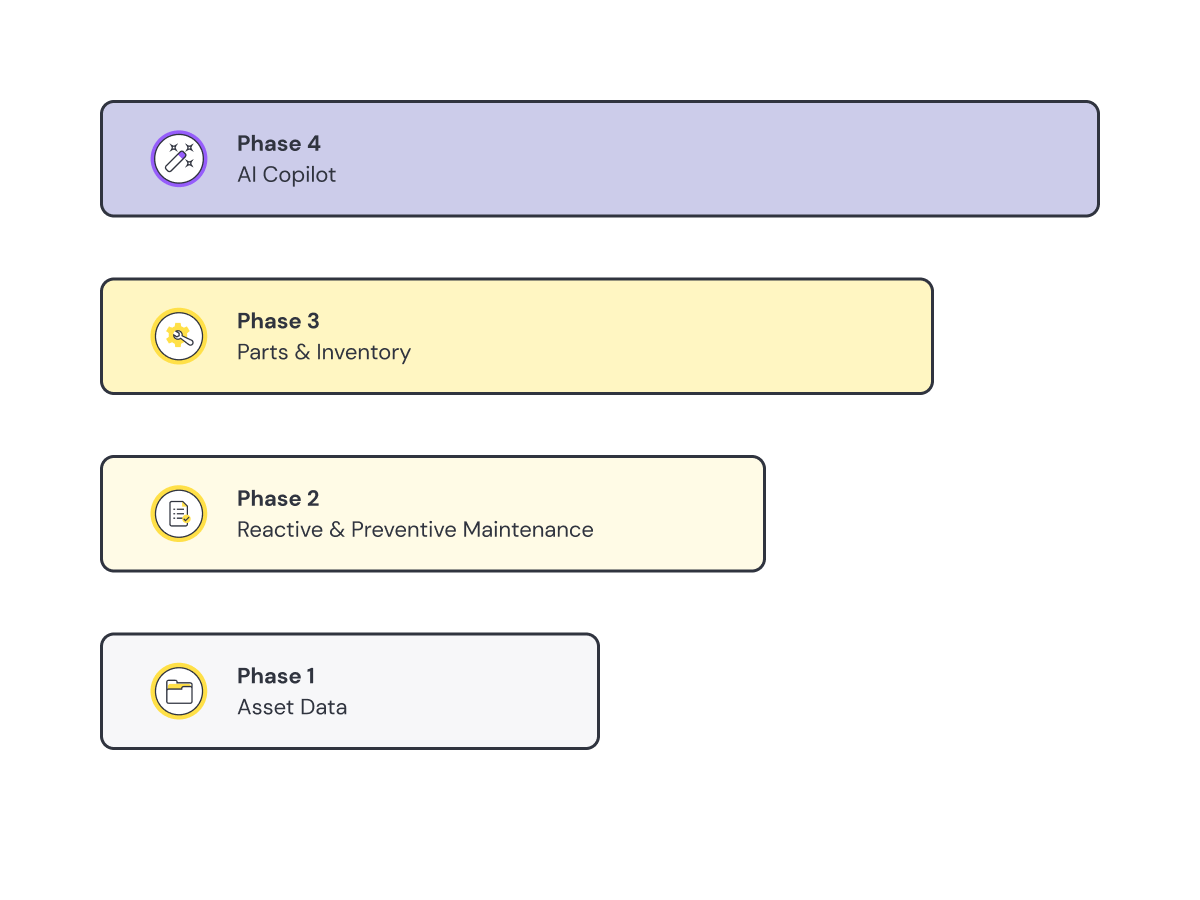
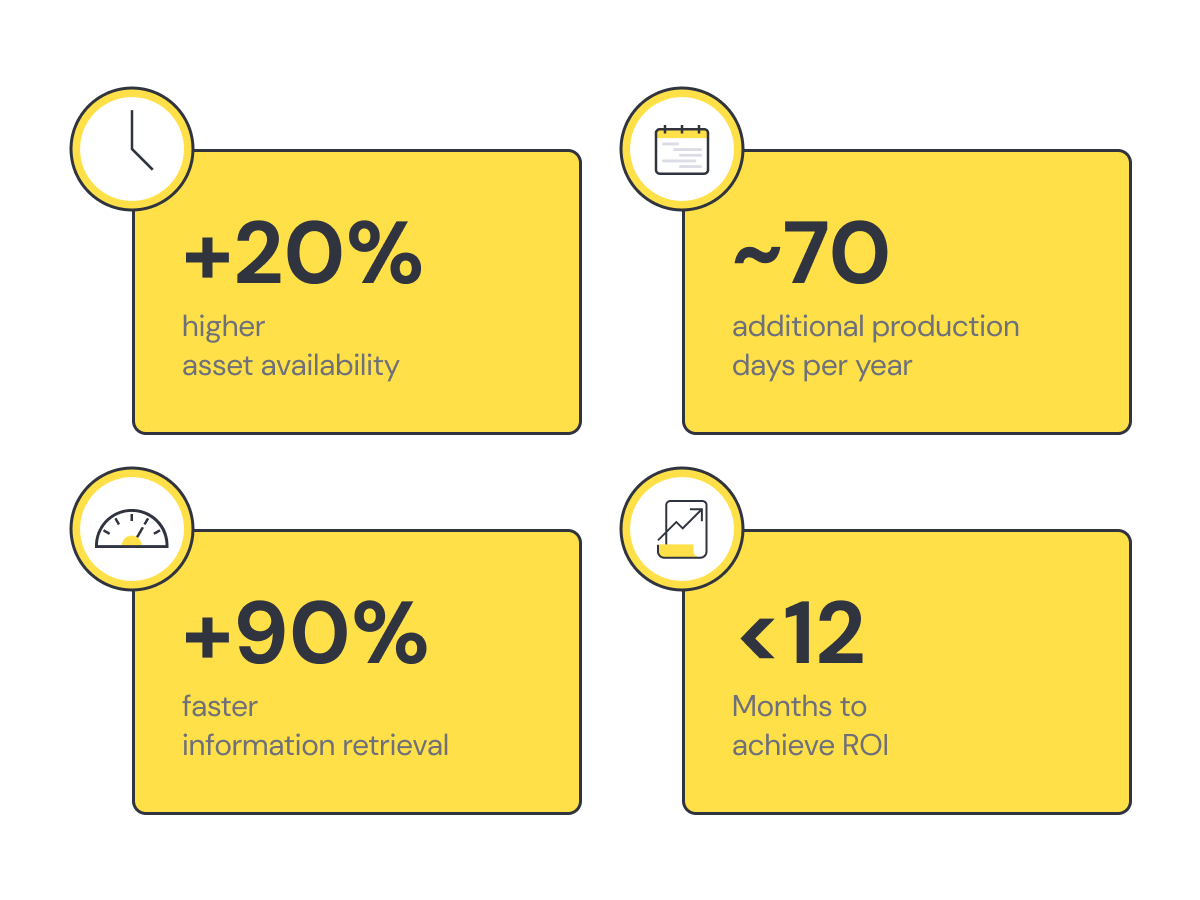
Tangible results – measurable impact
After one year with the remberg maintenance software, Plant Manager Christian Texter sums it up:
- +20% asset availability – that’s around 70 additional production days per year
- 90% faster access to information
- Shorter MTTR thanks to clear spare parts management
- ROI in under twelve months – without added IT workload, since the platform runs in the cloud
- Audit prep in hours instead of days – all supplier and product documentation is stored centrally and digitally
Outlook & next steps
These results didn’t go unnoticed: at Maintainer 2025, the annual event for the maintenance industry, a renowned jury honored deputy maintenance manager Patrick Längler for introducing and using the AI Copilot at Meguin. They praised “the leap from zero digitization to AI-assisted maintenance in record time” – a strong signal that true innovation isn’t about company size.
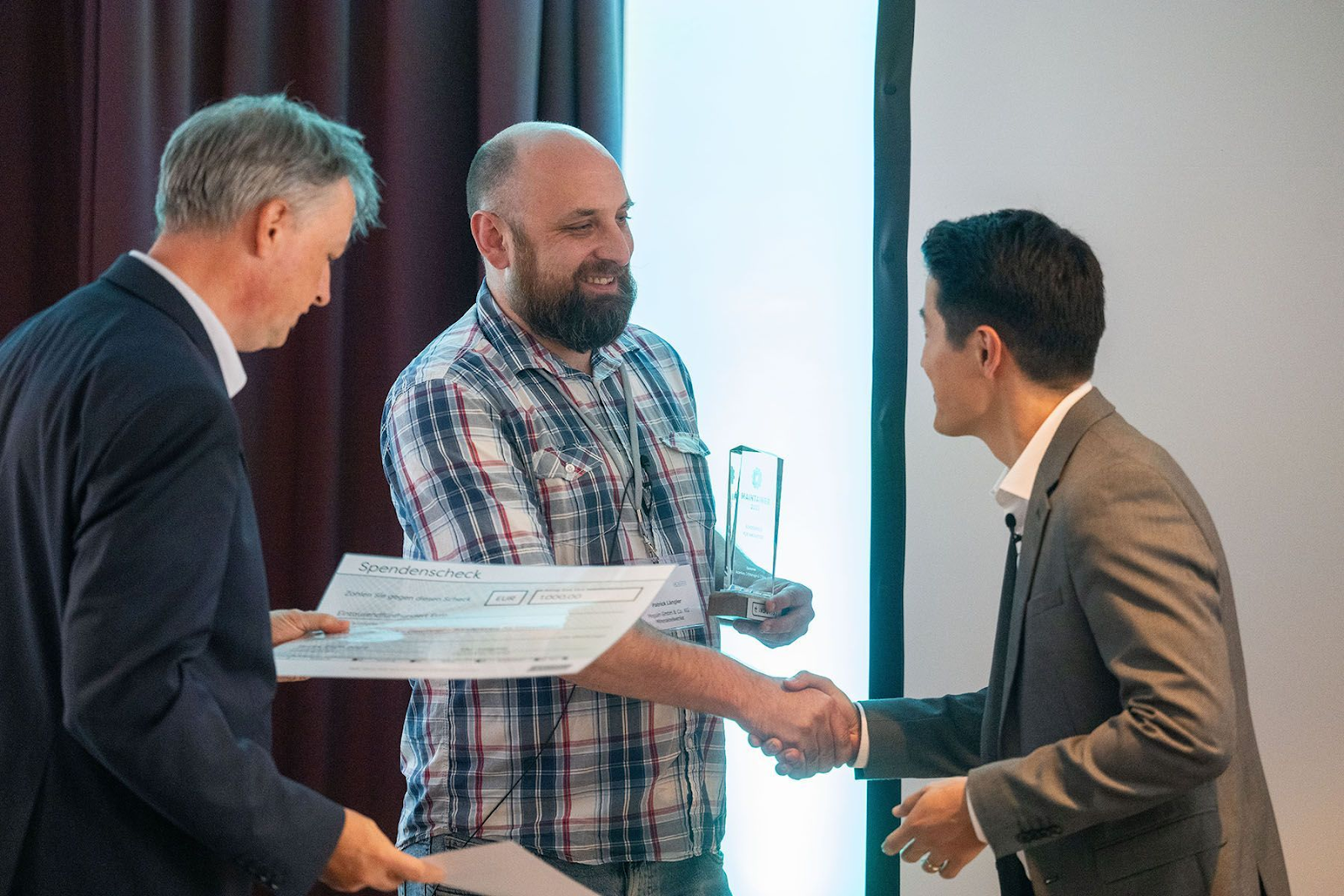
But Meguin isn’t stopping there. Plant Manager Christian Texter and his team are already focused on the next milestones:
- Implement predictive maintenance – Live sensor data from filling lines will automatically detect anomalies, schedule maintenance proactively, and boost asset availability even further
- Expand knowledge sharing – Every new insight flows into the remberg maintenance software, so new technicians can get up to speed faster and the growing skills gap is tackled head-on
Meguin stays true to its strategy: practical digitization, measurable impact at every stage – and eyes always on what’s next.
Unlock the Full Potential of Your Assets, Equipment & Facilities
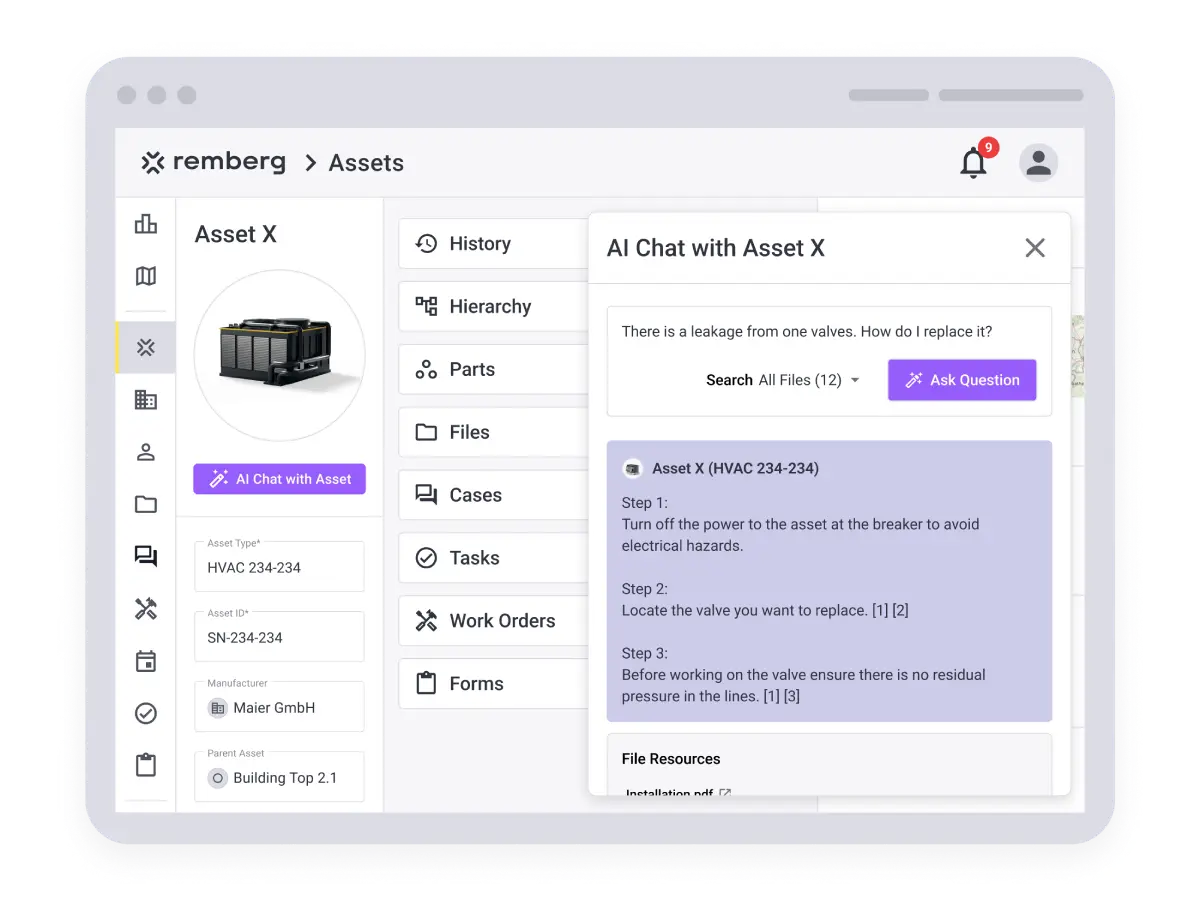
Newsletter
Inspiring content, trends & news.